汽車輕量化有什么缺點?有人這么回答:缺點是很多消費者認為車越重越好。
實際上,車身的輕重與安全性并沒有很強的相關性。甚至有研究數(shù)據(jù)表明,車身減重有時還有助于提高車輛的安全性。
作為汽車行業(yè)的重要發(fā)展方向,輕量化可以在保障汽車強度和安全性能的前提下,通過降低汽車的重量,提高汽車的動力性,減少燃料消耗,降低排放。
一組數(shù)據(jù)可以很好地說明輕量化技術對于汽車節(jié)能和環(huán)保的意義:汽車整車重量如果減少10%,就可以實現(xiàn)節(jié)油6%-8%,百公里油耗降低0.3升-0.6升,二氧化碳排放降低5克-8克。
當下車企紛紛加碼輕量化,可以說主要驅動力就是日漸嚴苛的油耗和排放法規(guī)。我國規(guī)定,2020年當年產(chǎn)乘用車平均燃料消耗降至5升/百公里。另外,根據(jù)規(guī)劃,汽車產(chǎn)業(yè)碳排放總量先于國家承諾和產(chǎn)業(yè)規(guī)模,于2028年率先達到峰值。
當前汽車行業(yè)輕量化的途徑主要有這三個方面:一是結構設計的優(yōu)化,二是采用輕量化的材料,三是輕量化材料的成型技術。顯然,材料對于輕量化的最終實現(xiàn)非常關鍵。
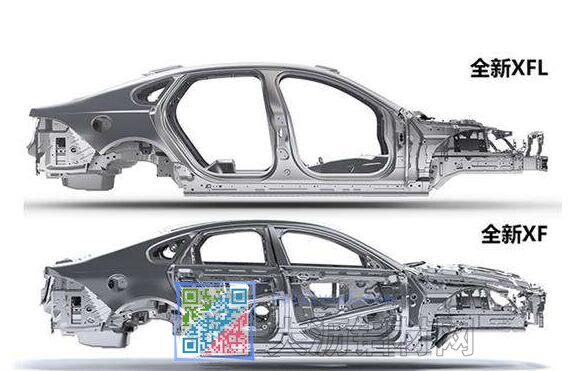
目前常見的輕量化材料主要包括鋁合金、鎂合金、高強度鋼等金屬材料以及碳纖維、塑料等非金屬復合材料等。
由于不同材料和工藝的成本存在不小差異,不同價位的車也會選擇不同的輕量化解決方案。比如碳纖維是成本相對較高的輕量化材料,主要用于高端車型比如跑車上。
而與碳纖維復合材料相比,鋁合金不但有成本優(yōu)勢,再制造、再利用也更加容易,相關技術也比較成熟,在汽車材料中是應用最多的輕質材料。
從減重效果上來看,鋁合金優(yōu)于鋼鐵,汽車使用1公斤鋁合金相當于2.25公斤的鋼鐵。和鋼鐵材料相比,鋁合金還有熱導率高、耐腐蝕性好、易加工、具有良好的吸能性等優(yōu)點。
但事實上,目前鋁作為輕量化材料主要還是應用在高端車型上,比如奧迪A8、捷豹XFL、特斯拉等都推出全鋁車身。除了成本問題,還因為全鋁車身的加工工藝存在很高的技術門檻,很多車企望而卻步。
直到2016年4月7日,我國第一家專制全鋁車身車間在奇瑞捷豹路虎常熟工廠竣工投產(chǎn)。同年8月推出的全新捷豹XFL,也成為第一款在中國本地生產(chǎn)制造的全鋁車身車型。
今年4月7日,恰逢奇瑞捷豹路虎全鋁車身車間竣工一周年之際,《汽車商業(yè)評論》在常熟基地參加了奇瑞捷豹路虎全鋁技術之旅,近距離了解這家公司的全鋁制造技術,以及這項技術本地化落地的來之不易。

天氣也會成為問題
在2015年9月?lián)纹嫒鸾荼坊⒐境崭笨偛弥埃愌┓迨浅J焐a(chǎn)基地的負責人。他告訴《汽車商業(yè)評論》,當年他帶領團隊在策劃、建設全鋁車身專制車間的時候,壓力非常大。
奇瑞捷豹路虎常務副總裁陳雪峰稱,經(jīng)銷商的鋁車身處理經(jīng)驗也是奇瑞捷豹路虎在鋁車身領域的核心競爭力。
由于鋁材是冷連接的機械連接方式,從鉚釘、鉚模、設備、原材料、板材到不同材質的搭接來講,要求非常高,一開始陳雪峰的團隊就面臨了三大領域的挑戰(zhàn)。
第一,在模具的開發(fā)過程中,拔模深度、拔模倒角、沖材速度等因素至關重要,而國內很多供應商對于鋁車身成型的這種經(jīng)驗積累還遠遠不夠。
第二,原材料國產(chǎn)化以后,可能由于環(huán)境問題,材料的特性和歐洲有一些差異,這就需要對鉚接參數(shù)進行調整,他們花了三個月時間來調整鉚釘和鉚模。
第三,生產(chǎn)過程管理以及質量管理。與焊裝要進行設備測試檢查不同,鋁車身更多依賴于目測,這就需要有非常多的數(shù)據(jù)來證實這種檢測方式是沒問題的。
全鋁車身的出爐需要整個汽車制造供應鏈的密切配合,奇瑞捷豹路虎與全球多家知名供應商展開合作,共同解決鋁制技術本地化過程中遇到的難題。
全球知名鋁壓延產(chǎn)品制造商諾貝麗斯(Novelis)為奇瑞捷豹路虎全鋁車身車間供應鋁材。諾貝麗斯常州工廠,也即中國第一家汽車鋁板生產(chǎn)廠商,于2014年10月21日竣工投產(chǎn)。這個日子恰巧與奇瑞捷豹路虎常熟工廠開業(yè)的日子重合。
全新捷豹XFL所應用的絕大多數(shù)汽車鋁材都來自諾貝麗斯常州工廠,剩下的部分則來自諾貝麗斯瑞士西耶爾(Sierre)工廠。
首先要進行材料的本地化。按照奇瑞捷豹路虎高級工程師王勛奇的說法,整個車身要達到鋼性需求和扭曲強度要求才能保證乘客的安全,這樣反推材料,首先要保證材料的穩(wěn)定性,另外,材料經(jīng)過鉚接和涂裝烘烤之后整體的性能達到要求的剛性和扭曲強度。
所有的諾貝麗斯供給奇瑞捷豹路虎的材料,都要經(jīng)過奇瑞捷豹路虎的材料驗證,當時技術團隊針對諾貝麗斯的板材在國內不同的特性做了國產(chǎn)化的測試,這些驗證都要拿到歐洲做。
由于英國的材料供貨周期和國內的供貨周期不一樣,以AC600材料為例,這個吸能材料通常是六個月的有效期,過了有效期材料會逐步硬化。諾貝麗斯中國技術支持工程師曹龍兵說:“我們的材料強度、耐腐蝕性能等有些指標甚至要高于歐洲的指標。”
這些還僅僅是局限于現(xiàn)在能夠本地化的一些材料,有一些高性能的材料目前還達不到國產(chǎn)化的水平。
全新捷豹XFL使用的膠黏劑則由全球專業(yè)化工品生產(chǎn)商西卡(SIKA)提供,包括結構膠、玻璃膠、減振膠等產(chǎn)品全部原裝進口。
由于中英的氣候存在差異,西卡也遇到了諾貝麗斯同樣的有效期問題。英國氣溫波動不大,而中國冬冷夏熱,玻璃底涂有效期在英國是三個月,但到了中國,他們做了很多本地化匹配驗證實驗之后發(fā)現(xiàn),有效期縮短到一到兩個月。
這對西卡、奇瑞捷豹路虎以及供應商物流環(huán)節(jié)都提出一個挑戰(zhàn)。首先是零庫存,第二,要考慮怎樣有效地在盡可能短的時間內把產(chǎn)品用在車身上,以達到非常好的性能。
前期西卡做了很多匹配性實驗,包括配合鉚接工藝做粘接實驗、老化實驗,還做國外材質和國內材質的橫向比較,確保產(chǎn)品性能和國外一模一樣。
作為奇瑞捷豹路虎的供應商,西卡在參與全鋁車身項目的過程中也有了意外收獲:做了很多測試,積累了不同溫度和濕度條件下的數(shù)據(jù),甚至歐洲的團隊也開始找他們要數(shù)據(jù),要求輸送經(jīng)驗。
不是一般的國產(chǎn)化
鋁材可以做汽車白車身、結構件、覆蓋件,“從難易程度來講,覆蓋件比較容易做,比如發(fā)動機發(fā)罩內外板、四門兩蓋。但是鋁要做汽車白車身和結構件,涉及金屬連接技術、深沖壓技術,技術難度比較高”。
諾貝麗斯中國區(qū)董事總經(jīng)理兼諾貝麗斯亞洲汽車業(yè)務副總裁劉清曾這樣告訴《汽車商業(yè)評論》。
為實現(xiàn)最佳車身性能,奇瑞捷豹路虎挑選不同系列、不同特點的高強度鋁合金材料,如AC170、AC300、AC600、RC5754和5182,應用于智能全鋁車身架構。
RC5754在強度、耐腐蝕性、連接性及成型性等方面表現(xiàn)出眾,車身多處都有應用。AC600鋁合金適用于車身加強件,AC300鋁合金用于防撞梁結構,AC170鋁合金適用于外板包邊和側圍的覆蓋件。
在全鋁車身生產(chǎn)中,除了性能優(yōu)越的鋁材,還需要有先進的連接技術。
全新捷豹XFL車身有2754個鉚點,采用了18種鉚模、30種鉚釘,定制匹配480種板材搭接,采用了從航空領域引入的自沖鉚接技術(self pierce riveting,簡稱SPR)。
這種技術是通過伺服電機提供動力將鉚釘直接壓入待鉚接板材,壓力高達60-80KN,然后鉚接板材在鉚釘?shù)膲毫ο潞豌T釘發(fā)生塑性形變,充盈于鉚模之中。
自沖鉚接為冷連接技術,是目前汽車制造行業(yè)車身連接工藝中最為環(huán)保的連接方式之一。車身連接處不會產(chǎn)生熱變形,無飛濺產(chǎn)生,僅需氣源,無需循環(huán)水冷卻,整個過程無任何污染物產(chǎn)生,比傳統(tǒng)焊接節(jié)能70%。
奇瑞捷豹路虎與英國的亨羅布(Henrob)公司在自沖鉚接技術上進行合作。成立于1985年的亨羅布是SPR技術發(fā)明人及市場引領者,2016年占全球市場份額60%左右。
來自亨羅布的一組數(shù)據(jù)顯示,全球2016年銷售的9300萬輛汽車中大約有6%應用SPR技術,這些數(shù)字到2021年將分別達到1.02億輛和11%。而與奇瑞捷豹路虎常熟工廠合作,是亨羅布第一次在中國大規(guī)模使用SPR工藝。
亨羅布中國副總經(jīng)理高恩興有很深的體驗,“在本地化的過程中,不僅僅是拷貝國外的材料拿過來直接用,而是要讓材料和技術應用本地化,形成一個戰(zhàn)略型的合作和技術本地化升級”。
由于方方面面的原因,國內與國外兩邊的板材材料不一樣,需要通過調整鉚接參數(shù)來實現(xiàn)板材的穩(wěn)定性。亨羅布經(jīng)過數(shù)月的調整,為所有板材都找到了相對應的鉚釘鉚模解決方案。
另外,亨羅布團隊還面臨這樣的挑戰(zhàn):整個工藝順序和國外不一樣。在國外捷豹路虎用了300多套系統(tǒng)的生產(chǎn)線,常熟工廠有232個鉚槍,兩種鉚釘一種模具要解決所有覆蓋區(qū)域的各種各樣的板材組合,面對的復雜局面更多。
與自沖鉚接相配合的還有一項鉚接膠合技術,自沖鉚接與車身結構黏合劑的組合,將車身連接強度增大至單純鉚接強度的2至3倍。《汽車商業(yè)評論》了解到,鉚接膠合技術在奇瑞捷豹路虎全鋁車身連接工藝中占比達72%。
奇瑞捷豹路虎常熟工廠全鋁車身車間擁有335臺機器人,其中自沖鉚接機器人數(shù)量為232套,實現(xiàn)智能全鋁車身架構100%自動化生產(chǎn)。而且,全鋁車間設有專用鋁余料回收系統(tǒng),可以實現(xiàn)鋁廢料100%回收。
為全方位實時監(jiān)測全鋁車身的制造品質,奇瑞捷豹路虎全鋁車身車間還擁有一套過程質量保證體系,包括自沖鉚接的適時過程監(jiān)控、可視化涂膠監(jiān)測系統(tǒng)、激光在線精度測量控制系統(tǒng)、鉚接點的無損檢測和破壞性測試等。
在此基礎上打造出的奇瑞捷豹路虎智能全鋁車身架構,要比同等結構的鋼車身減重20%-45%,靜態(tài)剛度增加20%以上。
全新捷豹XFL的鋁合金含量達到了國內最高75%的比率,白車身重量297kg,其一體式?jīng)_壓側圍重量僅7公斤,而且保持了進口版車型近50:50的完美前后配重,帶來了更短的制動距離、更精準的操控,降低了車的能耗和排放。
“我們已經(jīng)有非常高的信心來處理和管理產(chǎn)品,這個過程和一般所說的產(chǎn)品國產(chǎn)化還不太一樣,這是技術的國產(chǎn)化。技術國產(chǎn)化的難度遠高于單純的產(chǎn)品國產(chǎn)化。”奇瑞捷豹路虎常務副總裁陳雪峰如此表示。
全鋁車間在常熟落地,奇瑞捷豹路虎也是第一次培養(yǎng)自己的鋁車身專家,人員的知識積累水平,以及整個供應體系的成熟程度,都得到很大提升。
陳雪峰告訴《汽車商業(yè)評論》,“到今天我們已經(jīng)達到和超越了捷豹路虎全球的質量標準,目前也在全面穩(wěn)定地運行當中。”
售后服務同樣重要
國內,鋁材做汽車白車身、結構件和覆蓋件,最開始是歐美一些合資企業(yè)把CKD件運到中國進行組裝。發(fā)展到第二階段本地化生產(chǎn),差不多有六年時間。
在整個推進鋁材技術本地化落地的過程中,奇瑞捷豹路虎主要做了三件事情:控制質量,持續(xù)加大國產(chǎn)化的成本控制,進一步提升服務水平。
捷豹路虎使用鋁材技術已經(jīng)有幾十年歷史,有一套非常成熟的售后服務理念和一些應對措施,可以為消費者提供更便捷同時更節(jié)約費用的售后維修服務。
首先,從維修的便捷性來考慮。從車身角度,他們對四門兩蓋這些容易受到破壞的區(qū)域進行模塊化的售后備件的設計。一旦需要維修就不必把整個側圍全換掉,而可能是局部進行換裝。同時,他們通過售后件的測試來確保在正規(guī)渠道維修的車輛的機械性能和安全性能,包括外觀美觀性也不會受到影響。
另外,在消費者關心的維修費用上,奇瑞捷豹路虎和保險公司有多種售后備件的金融解決辦法,讓顧客可能會有略微高點的費用,但是不像想象中的難以接受。
從2003年起,捷豹路虎就已經(jīng)向中國大量進口全鋁車身車型。因此,陳雪峰說,“對于合資公司來說,XFL是我們投放的第一款全鋁車身轎車,但是對于奇瑞捷豹路虎的經(jīng)銷商來說,他們已經(jīng)具備非常多的鋁車身處理經(jīng)驗。”
他認為,經(jīng)銷商積累的這種鋁車身處理經(jīng)驗也是奇瑞捷豹路虎在鋁車身領域的核心競爭力。因為競爭對手要熟練應用鋁車身的售后維修技術,并不是短時間內就可以實現(xiàn)的。
2016中國汽車工程學會年會發(fā)布了我國節(jié)能與新能源汽車技術路線圖,其中關于汽車輕量化技術的發(fā)展思路是三個階段逐步實現(xiàn)輕量化目標:
第一階段為2016年-2020年,實現(xiàn)整車比2015年減重10%。
重點發(fā)展超高強度鋼和先進高強度鋼技術,包括材料性能開發(fā),輕量化設計方法,成型技術,焊接工藝和測試評價方法等,實現(xiàn)高強度鋼在汽車應用比例達到50%以上,開展鋁合金板材沖壓制作技術研究并在車身實踐,研究不同材料的連接技術。
第二階段為2021年-2025年,實現(xiàn)整車比2015年減重20%。
以第三代汽車鋼和鋁合金技術為主線,實現(xiàn)鋼鋁等多種材料混合車身,全鋁車身的大范圍應用,實現(xiàn)鋁合金覆蓋件和鋁合金零部件的批量生產(chǎn)和產(chǎn)業(yè)化應用,同時加大對鎂合金和碳纖維復合材料零部件生產(chǎn)制造技術的開發(fā),增加鎂合金和碳纖維零部件的應用比例,單車用鋁量達到350kg。
第三階段為2026年-2030年,實現(xiàn)整車比2015年減重35%。
重點發(fā)展鎂合金和碳纖維復合材料技術,解決鎂合金及復合材料循環(huán)再利用問題,實現(xiàn)碳纖維復合材料混合車身及碳纖維零部件的大范圍應用,突破復雜零件成型技術和異種零件連接技術。單車用鎂合金達到45kg,碳纖維使用量占車重5%。
按照規(guī)劃,全鋁車身大范圍應用的時間是2021年-2025年。以此為參照,可以說,奇瑞捷豹路虎常熟工廠的全鋁車身車間很大程度上推進了中國汽車輕量化的進程,其鋁材技術在中國落地生根,也為行業(yè)提供了可供借鑒的本土化經(jīng)驗。
實際上,車身的輕重與安全性并沒有很強的相關性。甚至有研究數(shù)據(jù)表明,車身減重有時還有助于提高車輛的安全性。
作為汽車行業(yè)的重要發(fā)展方向,輕量化可以在保障汽車強度和安全性能的前提下,通過降低汽車的重量,提高汽車的動力性,減少燃料消耗,降低排放。
一組數(shù)據(jù)可以很好地說明輕量化技術對于汽車節(jié)能和環(huán)保的意義:汽車整車重量如果減少10%,就可以實現(xiàn)節(jié)油6%-8%,百公里油耗降低0.3升-0.6升,二氧化碳排放降低5克-8克。
當下車企紛紛加碼輕量化,可以說主要驅動力就是日漸嚴苛的油耗和排放法規(guī)。我國規(guī)定,2020年當年產(chǎn)乘用車平均燃料消耗降至5升/百公里。另外,根據(jù)規(guī)劃,汽車產(chǎn)業(yè)碳排放總量先于國家承諾和產(chǎn)業(yè)規(guī)模,于2028年率先達到峰值。
當前汽車行業(yè)輕量化的途徑主要有這三個方面:一是結構設計的優(yōu)化,二是采用輕量化的材料,三是輕量化材料的成型技術。顯然,材料對于輕量化的最終實現(xiàn)非常關鍵。
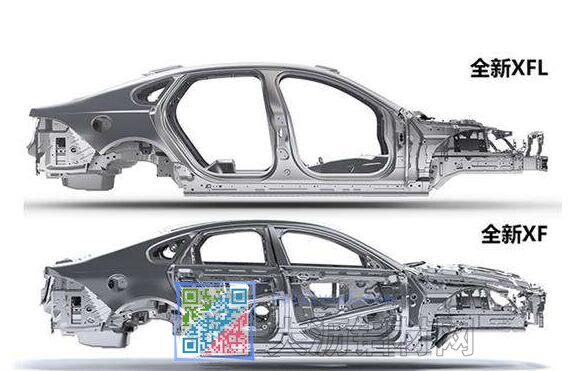
目前常見的輕量化材料主要包括鋁合金、鎂合金、高強度鋼等金屬材料以及碳纖維、塑料等非金屬復合材料等。
由于不同材料和工藝的成本存在不小差異,不同價位的車也會選擇不同的輕量化解決方案。比如碳纖維是成本相對較高的輕量化材料,主要用于高端車型比如跑車上。
而與碳纖維復合材料相比,鋁合金不但有成本優(yōu)勢,再制造、再利用也更加容易,相關技術也比較成熟,在汽車材料中是應用最多的輕質材料。
從減重效果上來看,鋁合金優(yōu)于鋼鐵,汽車使用1公斤鋁合金相當于2.25公斤的鋼鐵。和鋼鐵材料相比,鋁合金還有熱導率高、耐腐蝕性好、易加工、具有良好的吸能性等優(yōu)點。
但事實上,目前鋁作為輕量化材料主要還是應用在高端車型上,比如奧迪A8、捷豹XFL、特斯拉等都推出全鋁車身。除了成本問題,還因為全鋁車身的加工工藝存在很高的技術門檻,很多車企望而卻步。
直到2016年4月7日,我國第一家專制全鋁車身車間在奇瑞捷豹路虎常熟工廠竣工投產(chǎn)。同年8月推出的全新捷豹XFL,也成為第一款在中國本地生產(chǎn)制造的全鋁車身車型。
今年4月7日,恰逢奇瑞捷豹路虎全鋁車身車間竣工一周年之際,《汽車商業(yè)評論》在常熟基地參加了奇瑞捷豹路虎全鋁技術之旅,近距離了解這家公司的全鋁制造技術,以及這項技術本地化落地的來之不易。

天氣也會成為問題
在2015年9月?lián)纹嫒鸾荼坊⒐境崭笨偛弥埃愌┓迨浅J焐a(chǎn)基地的負責人。他告訴《汽車商業(yè)評論》,當年他帶領團隊在策劃、建設全鋁車身專制車間的時候,壓力非常大。
奇瑞捷豹路虎常務副總裁陳雪峰稱,經(jīng)銷商的鋁車身處理經(jīng)驗也是奇瑞捷豹路虎在鋁車身領域的核心競爭力。
由于鋁材是冷連接的機械連接方式,從鉚釘、鉚模、設備、原材料、板材到不同材質的搭接來講,要求非常高,一開始陳雪峰的團隊就面臨了三大領域的挑戰(zhàn)。
第一,在模具的開發(fā)過程中,拔模深度、拔模倒角、沖材速度等因素至關重要,而國內很多供應商對于鋁車身成型的這種經(jīng)驗積累還遠遠不夠。
第二,原材料國產(chǎn)化以后,可能由于環(huán)境問題,材料的特性和歐洲有一些差異,這就需要對鉚接參數(shù)進行調整,他們花了三個月時間來調整鉚釘和鉚模。
第三,生產(chǎn)過程管理以及質量管理。與焊裝要進行設備測試檢查不同,鋁車身更多依賴于目測,這就需要有非常多的數(shù)據(jù)來證實這種檢測方式是沒問題的。
全鋁車身的出爐需要整個汽車制造供應鏈的密切配合,奇瑞捷豹路虎與全球多家知名供應商展開合作,共同解決鋁制技術本地化過程中遇到的難題。
全球知名鋁壓延產(chǎn)品制造商諾貝麗斯(Novelis)為奇瑞捷豹路虎全鋁車身車間供應鋁材。諾貝麗斯常州工廠,也即中國第一家汽車鋁板生產(chǎn)廠商,于2014年10月21日竣工投產(chǎn)。這個日子恰巧與奇瑞捷豹路虎常熟工廠開業(yè)的日子重合。
全新捷豹XFL所應用的絕大多數(shù)汽車鋁材都來自諾貝麗斯常州工廠,剩下的部分則來自諾貝麗斯瑞士西耶爾(Sierre)工廠。
首先要進行材料的本地化。按照奇瑞捷豹路虎高級工程師王勛奇的說法,整個車身要達到鋼性需求和扭曲強度要求才能保證乘客的安全,這樣反推材料,首先要保證材料的穩(wěn)定性,另外,材料經(jīng)過鉚接和涂裝烘烤之后整體的性能達到要求的剛性和扭曲強度。
所有的諾貝麗斯供給奇瑞捷豹路虎的材料,都要經(jīng)過奇瑞捷豹路虎的材料驗證,當時技術團隊針對諾貝麗斯的板材在國內不同的特性做了國產(chǎn)化的測試,這些驗證都要拿到歐洲做。
由于英國的材料供貨周期和國內的供貨周期不一樣,以AC600材料為例,這個吸能材料通常是六個月的有效期,過了有效期材料會逐步硬化。諾貝麗斯中國技術支持工程師曹龍兵說:“我們的材料強度、耐腐蝕性能等有些指標甚至要高于歐洲的指標。”
這些還僅僅是局限于現(xiàn)在能夠本地化的一些材料,有一些高性能的材料目前還達不到國產(chǎn)化的水平。
全新捷豹XFL使用的膠黏劑則由全球專業(yè)化工品生產(chǎn)商西卡(SIKA)提供,包括結構膠、玻璃膠、減振膠等產(chǎn)品全部原裝進口。
由于中英的氣候存在差異,西卡也遇到了諾貝麗斯同樣的有效期問題。英國氣溫波動不大,而中國冬冷夏熱,玻璃底涂有效期在英國是三個月,但到了中國,他們做了很多本地化匹配驗證實驗之后發(fā)現(xiàn),有效期縮短到一到兩個月。
這對西卡、奇瑞捷豹路虎以及供應商物流環(huán)節(jié)都提出一個挑戰(zhàn)。首先是零庫存,第二,要考慮怎樣有效地在盡可能短的時間內把產(chǎn)品用在車身上,以達到非常好的性能。
前期西卡做了很多匹配性實驗,包括配合鉚接工藝做粘接實驗、老化實驗,還做國外材質和國內材質的橫向比較,確保產(chǎn)品性能和國外一模一樣。
作為奇瑞捷豹路虎的供應商,西卡在參與全鋁車身項目的過程中也有了意外收獲:做了很多測試,積累了不同溫度和濕度條件下的數(shù)據(jù),甚至歐洲的團隊也開始找他們要數(shù)據(jù),要求輸送經(jīng)驗。
不是一般的國產(chǎn)化
鋁材可以做汽車白車身、結構件、覆蓋件,“從難易程度來講,覆蓋件比較容易做,比如發(fā)動機發(fā)罩內外板、四門兩蓋。但是鋁要做汽車白車身和結構件,涉及金屬連接技術、深沖壓技術,技術難度比較高”。
諾貝麗斯中國區(qū)董事總經(jīng)理兼諾貝麗斯亞洲汽車業(yè)務副總裁劉清曾這樣告訴《汽車商業(yè)評論》。
為實現(xiàn)最佳車身性能,奇瑞捷豹路虎挑選不同系列、不同特點的高強度鋁合金材料,如AC170、AC300、AC600、RC5754和5182,應用于智能全鋁車身架構。
RC5754在強度、耐腐蝕性、連接性及成型性等方面表現(xiàn)出眾,車身多處都有應用。AC600鋁合金適用于車身加強件,AC300鋁合金用于防撞梁結構,AC170鋁合金適用于外板包邊和側圍的覆蓋件。
在全鋁車身生產(chǎn)中,除了性能優(yōu)越的鋁材,還需要有先進的連接技術。
全新捷豹XFL車身有2754個鉚點,采用了18種鉚模、30種鉚釘,定制匹配480種板材搭接,采用了從航空領域引入的自沖鉚接技術(self pierce riveting,簡稱SPR)。
這種技術是通過伺服電機提供動力將鉚釘直接壓入待鉚接板材,壓力高達60-80KN,然后鉚接板材在鉚釘?shù)膲毫ο潞豌T釘發(fā)生塑性形變,充盈于鉚模之中。
自沖鉚接為冷連接技術,是目前汽車制造行業(yè)車身連接工藝中最為環(huán)保的連接方式之一。車身連接處不會產(chǎn)生熱變形,無飛濺產(chǎn)生,僅需氣源,無需循環(huán)水冷卻,整個過程無任何污染物產(chǎn)生,比傳統(tǒng)焊接節(jié)能70%。
奇瑞捷豹路虎與英國的亨羅布(Henrob)公司在自沖鉚接技術上進行合作。成立于1985年的亨羅布是SPR技術發(fā)明人及市場引領者,2016年占全球市場份額60%左右。
來自亨羅布的一組數(shù)據(jù)顯示,全球2016年銷售的9300萬輛汽車中大約有6%應用SPR技術,這些數(shù)字到2021年將分別達到1.02億輛和11%。而與奇瑞捷豹路虎常熟工廠合作,是亨羅布第一次在中國大規(guī)模使用SPR工藝。
亨羅布中國副總經(jīng)理高恩興有很深的體驗,“在本地化的過程中,不僅僅是拷貝國外的材料拿過來直接用,而是要讓材料和技術應用本地化,形成一個戰(zhàn)略型的合作和技術本地化升級”。
由于方方面面的原因,國內與國外兩邊的板材材料不一樣,需要通過調整鉚接參數(shù)來實現(xiàn)板材的穩(wěn)定性。亨羅布經(jīng)過數(shù)月的調整,為所有板材都找到了相對應的鉚釘鉚模解決方案。
另外,亨羅布團隊還面臨這樣的挑戰(zhàn):整個工藝順序和國外不一樣。在國外捷豹路虎用了300多套系統(tǒng)的生產(chǎn)線,常熟工廠有232個鉚槍,兩種鉚釘一種模具要解決所有覆蓋區(qū)域的各種各樣的板材組合,面對的復雜局面更多。
與自沖鉚接相配合的還有一項鉚接膠合技術,自沖鉚接與車身結構黏合劑的組合,將車身連接強度增大至單純鉚接強度的2至3倍。《汽車商業(yè)評論》了解到,鉚接膠合技術在奇瑞捷豹路虎全鋁車身連接工藝中占比達72%。
奇瑞捷豹路虎常熟工廠全鋁車身車間擁有335臺機器人,其中自沖鉚接機器人數(shù)量為232套,實現(xiàn)智能全鋁車身架構100%自動化生產(chǎn)。而且,全鋁車間設有專用鋁余料回收系統(tǒng),可以實現(xiàn)鋁廢料100%回收。
為全方位實時監(jiān)測全鋁車身的制造品質,奇瑞捷豹路虎全鋁車身車間還擁有一套過程質量保證體系,包括自沖鉚接的適時過程監(jiān)控、可視化涂膠監(jiān)測系統(tǒng)、激光在線精度測量控制系統(tǒng)、鉚接點的無損檢測和破壞性測試等。
在此基礎上打造出的奇瑞捷豹路虎智能全鋁車身架構,要比同等結構的鋼車身減重20%-45%,靜態(tài)剛度增加20%以上。
全新捷豹XFL的鋁合金含量達到了國內最高75%的比率,白車身重量297kg,其一體式?jīng)_壓側圍重量僅7公斤,而且保持了進口版車型近50:50的完美前后配重,帶來了更短的制動距離、更精準的操控,降低了車的能耗和排放。
“我們已經(jīng)有非常高的信心來處理和管理產(chǎn)品,這個過程和一般所說的產(chǎn)品國產(chǎn)化還不太一樣,這是技術的國產(chǎn)化。技術國產(chǎn)化的難度遠高于單純的產(chǎn)品國產(chǎn)化。”奇瑞捷豹路虎常務副總裁陳雪峰如此表示。
全鋁車間在常熟落地,奇瑞捷豹路虎也是第一次培養(yǎng)自己的鋁車身專家,人員的知識積累水平,以及整個供應體系的成熟程度,都得到很大提升。
陳雪峰告訴《汽車商業(yè)評論》,“到今天我們已經(jīng)達到和超越了捷豹路虎全球的質量標準,目前也在全面穩(wěn)定地運行當中。”
售后服務同樣重要
國內,鋁材做汽車白車身、結構件和覆蓋件,最開始是歐美一些合資企業(yè)把CKD件運到中國進行組裝。發(fā)展到第二階段本地化生產(chǎn),差不多有六年時間。
在整個推進鋁材技術本地化落地的過程中,奇瑞捷豹路虎主要做了三件事情:控制質量,持續(xù)加大國產(chǎn)化的成本控制,進一步提升服務水平。
捷豹路虎使用鋁材技術已經(jīng)有幾十年歷史,有一套非常成熟的售后服務理念和一些應對措施,可以為消費者提供更便捷同時更節(jié)約費用的售后維修服務。
首先,從維修的便捷性來考慮。從車身角度,他們對四門兩蓋這些容易受到破壞的區(qū)域進行模塊化的售后備件的設計。一旦需要維修就不必把整個側圍全換掉,而可能是局部進行換裝。同時,他們通過售后件的測試來確保在正規(guī)渠道維修的車輛的機械性能和安全性能,包括外觀美觀性也不會受到影響。
另外,在消費者關心的維修費用上,奇瑞捷豹路虎和保險公司有多種售后備件的金融解決辦法,讓顧客可能會有略微高點的費用,但是不像想象中的難以接受。
從2003年起,捷豹路虎就已經(jīng)向中國大量進口全鋁車身車型。因此,陳雪峰說,“對于合資公司來說,XFL是我們投放的第一款全鋁車身轎車,但是對于奇瑞捷豹路虎的經(jīng)銷商來說,他們已經(jīng)具備非常多的鋁車身處理經(jīng)驗。”
他認為,經(jīng)銷商積累的這種鋁車身處理經(jīng)驗也是奇瑞捷豹路虎在鋁車身領域的核心競爭力。因為競爭對手要熟練應用鋁車身的售后維修技術,并不是短時間內就可以實現(xiàn)的。
2016中國汽車工程學會年會發(fā)布了我國節(jié)能與新能源汽車技術路線圖,其中關于汽車輕量化技術的發(fā)展思路是三個階段逐步實現(xiàn)輕量化目標:
第一階段為2016年-2020年,實現(xiàn)整車比2015年減重10%。
重點發(fā)展超高強度鋼和先進高強度鋼技術,包括材料性能開發(fā),輕量化設計方法,成型技術,焊接工藝和測試評價方法等,實現(xiàn)高強度鋼在汽車應用比例達到50%以上,開展鋁合金板材沖壓制作技術研究并在車身實踐,研究不同材料的連接技術。
第二階段為2021年-2025年,實現(xiàn)整車比2015年減重20%。
以第三代汽車鋼和鋁合金技術為主線,實現(xiàn)鋼鋁等多種材料混合車身,全鋁車身的大范圍應用,實現(xiàn)鋁合金覆蓋件和鋁合金零部件的批量生產(chǎn)和產(chǎn)業(yè)化應用,同時加大對鎂合金和碳纖維復合材料零部件生產(chǎn)制造技術的開發(fā),增加鎂合金和碳纖維零部件的應用比例,單車用鋁量達到350kg。
第三階段為2026年-2030年,實現(xiàn)整車比2015年減重35%。
重點發(fā)展鎂合金和碳纖維復合材料技術,解決鎂合金及復合材料循環(huán)再利用問題,實現(xiàn)碳纖維復合材料混合車身及碳纖維零部件的大范圍應用,突破復雜零件成型技術和異種零件連接技術。單車用鎂合金達到45kg,碳纖維使用量占車重5%。
按照規(guī)劃,全鋁車身大范圍應用的時間是2021年-2025年。以此為參照,可以說,奇瑞捷豹路虎常熟工廠的全鋁車身車間很大程度上推進了中國汽車輕量化的進程,其鋁材技術在中國落地生根,也為行業(yè)提供了可供借鑒的本土化經(jīng)驗。