1 鋁型材的發展趨勢
隨著中國經濟建設的發展,中國建筑行業也迅猛的發展起來,鋁型材需求量也不斷地增加,型材的復雜程度不斷的加大。擠壓模具是鋁型材擠壓過程發生的場所,在鋁型材擠壓生產起到至關重要的作用,直接影響到擠壓產品的質量、決定了擠壓產品的形狀、尺寸精度及表面質量。復雜性使得鋁型材行業對模具的要求也不斷提高。合理的模具設計與制造加工是提高模具使用壽命的關鍵,提高模具使用壽命是產生生產效益的直接因素。
2 合理的模具設計
在設計、制造、生產的摸索與實踐中,從單孔型材模具到多孔型材模具的升級。如今本司成熟的多孔型材模具設計理念已成為提高產能的一種途徑,多孔型材模具成倍的產能遠遠超過以往單孔型材模具的生產效益值。使得多孔型材模具設計倍受歡迎,產品尺寸以及表面質量得到廣大客戶的認可,為本司提高生產效益作出了突出的貢獻。要生產出合格的產品必須采用合理的多孔型材模具設計與制造加工提高成品出材率,為達到客戶這一要求以及滿足在供貨期內客戶的需求量,模具設計理念與制造基點尤為重要。相對而言,多孔型材模具的整體強度比較薄弱,合理的模具設計參數對模具的使用壽命起著至關重要的作用。一般的單孔型材模具通常采用四孔四橋設計,這樣的設計在同行業比較常見也是相對穩定的。但遠遠達不到多孔型材模具成倍產能的優越性。與之而言多孔型材模具就不同于此。
2.1為考慮多孔模具腔中供料充分均勻及其平衡性。一模多腔必須采用多個料孔同時供料,這樣的模具多孔、多橋,以至于擠壓過程中傳遞給模具較高的壓力值,同時模具所承受的擠壓載荷也相應加重,而直接影響到模具的整體強度以及模具的使用壽命。為避免這一現象,可將設計的模具厚度減薄,減短金屬在料孔中的流動行程,模具料孔棱角加工全部以拋物線R角接順來降低料孔對金屬流動摩擦阻力(出料不穩定的情況下可適當加厚上模,保證其強度與剛度)。
2.2料孔面積的設計應遵循擠壓本身的原理
2.2.1靠近擠壓筒中心壓力值遠遠大于擠壓筒邊緣壓力值,所以接近邊緣的料孔與中心料孔要有相應的面積比例。為了保證邊緣與中心料孔供料的相對穩定,中心料孔設計為共用孔最好。與之對應的下模部分也應設計一定高度的欄基加以分腔與阻流,這樣可以使兩焊合室之間料流相對均勻不至于產生明顯流量差。
2.2.2料孔面積應盡可能的設計大些。如果在擠壓筒受限的情況下,可以將接近擠壓筒邊緣的料孔以擴孔的形式來滿足型材邊緣的供料,減少型材邊緣的流動阻力,達到同步出料減少型材偏壁的效果。同時也利于降低擠壓壓力、減輕對模具本身的受壓力提高模具使用壽命。
2.2.3為進一步減輕或避免中心與邊緣的壁厚差懸殊的現象,同時可將模芯向中心以X、Y軸橫縱向平移一定的理論壁厚尺寸控制。對于小模芯多孔型材模具,可想而知,這樣的型材極不穩定。由于模芯受料孔流量差以及焊合室內焊合壓力的影響,引起模芯側向受力不均而產生偏擺,出材后型材壁厚不均勻,懸殊較大。
a.設計的模芯角度可相應加大、下模焊合室相對做淺(陽極反應等表面處理應滿足有足夠焊合壓力 、保證其表面質量),從而避免模芯過長偏擺幅度過大,對薄壁料更是如此。
b.在保證模具強度的前提下料孔應盡可能接近型腔,以避免料孔離型腔過遠金屬流入型腔困難,出材后型材壁厚尺寸縮水過多達不到壁厚公差要求,在無法避免上述情形的情況下,以設計經驗也可將型材理論壁厚尺寸適當加厚加以調節。
2.2.4在一些非對稱的型材多孔模設計時,應充分考慮料孔與型腔的供料關系,正確放置料孔位置和選擇相應料孔的比例,以保證整個擠壓過程金屬流量的平衡和模芯四周受力的平衡。
2.2.5對于一些常規長腿的門窗穿膠料,往往會出現一些極其明顯的起坑、起骨等不良現象。為保證客戶高要求的型材表面質量,避免該現象的產生,模具橋位的設計應離開型材的分流部分與平模部分的“T”字交匯處擺放 ,同時將靠近此處平模部分的工作帶設計為無過渡或者減緩工作帶落差,過渡取值平緩、圓滑,這樣使得“T”處的供料更為充分、均勻,從而使該處型材組織性能得到更大的改善,有效避免了型材起坑、起骨等暗影的產生。
3 模具制造的優化
3.1在多孔模具的加工過程中,上模加工分兩面銑削加工。先加工入料面再從出料面用同一程式銑穿至入料面,這樣可以避免分流孔中間留下臺階,可以節約手工打磨時間,提高分流孔供料對稱性。更大程度上保證了模具供料的平衡性,這樣可使模具在擠壓的過程中出料的均衡性得到保障。
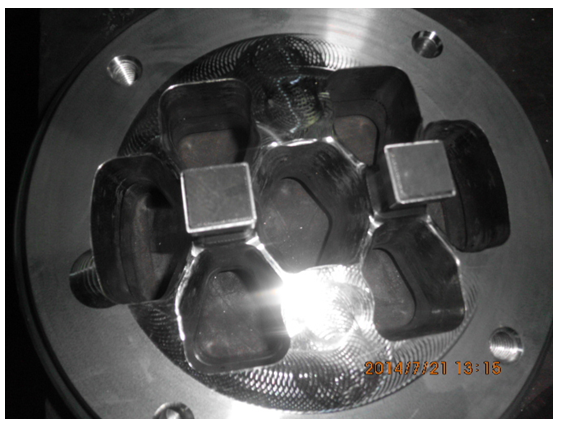
3.2在有導流的模具加工中,結合修模的實際經驗,運用三維實體軟件模擬出導流供料平衡的導流形狀,加工出標準仿形電極。利用標準仿形電極對模具導流部位逐一進行加工,確保多孔模具導流部位供料一致性,更進一步保證多孔模具的擠壓出料的平衡性。
3.3上模有螺絲位與釘位的下空刀處,通常電火花提高下空刀處會留下直角,不同的提高量會留下不同高度的直角位。工作帶出現明顯的直角過度,生產出來的型材表面大多會出現起坑、起骨的現象。為了避免這類現象的產生,利用加工中心定制T形刀具銑出下空刀高低位的工作帶斜線過渡,工作帶變成高低曲線連續過渡出料變得平穩。
有些模具設計出來模頸角度偏大,模頸過渡緩沖處較高。結合類似模具的返修方案及擠壓生產需求,結合實際效果模擬模具試模預判性。(例如:修改模芯角度實現金屬流動順暢性、修正制造加工工藝等等)
4 信息歸檔
對加工完成的模具實行存檔記錄、跟蹤試模、試模不合格返修、生產需求性。通過模具返修的信息進行拍照,對模具設計與加工存在的缺陷進行修正與存檔。進一步完善模具信息,整合出合理的設計與加工方式,為補充模具提供有圖有據的信息數據庫。
結束語:
擠壓模具設計及工藝優化、提高模具使用壽命、生產效益。通過模具制造工藝的優化、信息的建立及完善,設計圖紙的修改,整合出合理的模具設計及行之有效的加工方案。對提高模具使用壽命起著決定性作用,從而提高生產效益值。