眾所周知,鋁材擠壓模具最關鍵的部位是模孔的工作帶。其中工作帶的長度,角度,形狀和表面粗糙度是影響鋁型材成形和表面質量的關鍵因素。國內的擠壓廠目前都是依靠人工打磨拋光,借助于角規,刀口尺和千分尺來對工作帶的長度和表面進行檢測和修正,其精度往往難于保證,另外作業人員的技能水平差距也直接影響到作業后的效果,引入三坐標測量機后,如何提高修模作業者的水平,如何進行型材問題的模具分析是本文要向大家介紹的。
1 三坐標測量機的系統構成,測量原理和測量模型
1.1 硬件構成
三坐標測量機硬件系統由三坐標測量機,人工操作平臺,電腦控制系統和打印機組成。如圖1所示,探測臂上的探測頭可以在xyz三維空間移動和測量,電腦用于運行自動控制軟件和進行數據處理,打印機用于輸出測量結果。
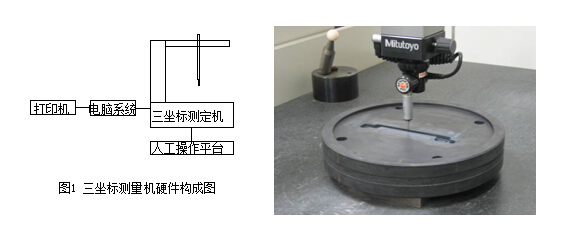
1.2軟件系統的測量原理和二次開發的測量模型
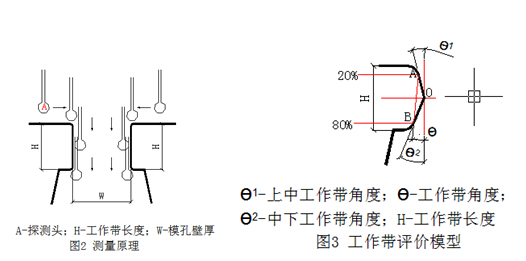
測量原理見圖2,先在模具表面建立測量基準平面,然后將探頭置于工作帶邊緣,啟動相應的探測程序,探測頭A沿著工作帶表面進行點掃描,記錄下每個點的坐標數據,測量終了后探測頭歸位,測量過程結束。
1.3工作帶評價的理論模型
根據實際使用中工作帶可能存在的形式,建立了一種評價理論模型,如圖3所示,為了表述工作帶輪廓形狀的好壞程度(平面度),我們將工作帶分為上中和中下兩部分進行評價,引入了角差概念,為減少測量誤差,計算時取工作帶長度的20%-80%范圍進行評估。
1.4 測量結果的表達和輸出
測量的坐標數據經電腦系統處理后生成直觀的文字和圖形的表達形式,由打印機進行輸出,易于對結果進行客觀分析,標準輸出結果如圖4所示:
輸出結果的信息包含:測量日期,模具型號,壁厚尺寸,工作帶長度,工作帶角度,上中工作帶角度,中下工作帶角度,角差,輪廓形狀圖。

1.5 對測量結果的評價標準
基于我廠對修模作業的要求,設定工作帶角度的作業標準為±0.05°管理范圍為±0.1°
角差管理范圍為±0.1°。超出此范圍的皆為不達標。
2 利用三坐標測量機幫助修模者提高作業水平
2.1 首先我們建立了一個作業測量記錄表,如圖5所示,圖中橫軸代表著檢測的工作帶角度誤差值,縱軸代表著表征工作帶平面度的角差值,圖中不同顏色的點代表著不同作業者拋光作業后的檢測結果。
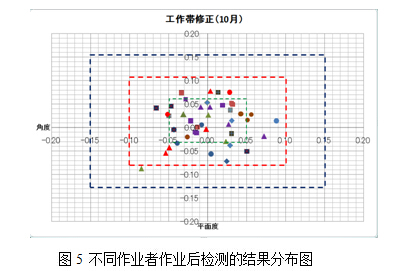
2.2建立作業檢測結果的評估等級,如圖6所示,A級,代表角度和角差均在±0.05°范圍內,B級,代表角度和角差均在±0.1°范圍內,C級,代表角度和角差均在±0.15°,對每位修模作業者要求每月自檢2-3套模具,空閑時可以自行進行練習。
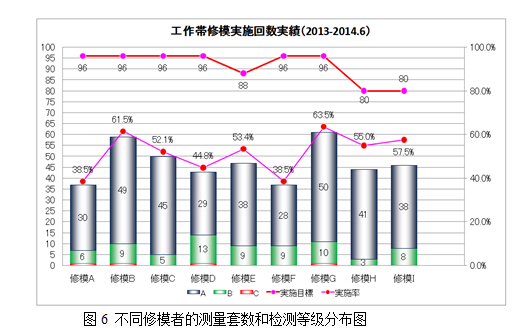
2.3上述模式在實施一年后所取得的效果,各位修模作業者技能水平都有了相當程度的提高,檢測結果A級達標率達到80%以上,更重要的收獲是擠壓模具上機中止率由原來33%降到了現在的15%左右。
3 三坐標測量機用于分析鋁材缺陷的模具問題的應用案例
擠壓模具在使用一段時間后,或者經多次拋光作業后工作帶都會出現不同程度的變形,如果能夠定期將使用中模具用三坐標機進行檢測,就能夠預早的發現問題,并進行修正,杜絕不良的型材問題發生。下面是集中常見的缺陷問題分析。
3.1鋁型材表面條紋增多,并伴有流點產生,將缺陷面模具工作帶用三坐標機進行檢測后發現工作帶塌邊較為嚴重,檢測結果如圖7所示,修正方法就是將工作帶打磨拋光還原到最初狀態。
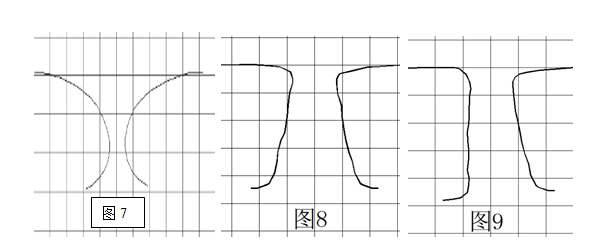
3.2多孔模具在使用一段時間以后出現了流速差,在排除了擠壓機對中問題后,用三坐標機對模具進行檢測,發現流速快的一孔工作帶下塌比較多,形成了明顯的負角度,如圖8所示,修正方法就是將負工作帶找正為90度,速差消除。
3.3 鋁型材出料平面波浪,平面凸,用三坐標機對模具進行檢測,發現波浪一側的工作帶產生了塌邊,如圖9所示,修正方法,將塌邊一側的工作帶修正為+0.2-+0.4度的正角度。
4 結束語
介紹三坐標測量機在擠壓修模中的應用方法,三坐標測量機可以在x,y,z三軸坐標空間進行任意點的坐標測定,測量精度可以達到1um,其應用軟件也功能強大,還可以方便的進行二次開發,應用于不同的場合,國內許多行業都用三坐標測量機作為產品終檢儀器。但在擠壓修模上的應用,本公司走在國內同行業的前面,對提高修模者作業水平和進行型材缺陷的模具分析提供了可靠地方法和手段。三坐標測量機在修模間實際使用中起到了相當大的作用,幫助修模者提高了自己的技能水平,并幫助修模者分析生產中的模具問題,為修模者提供可靠了分析數據,修模者還用來對日常使用的角規進行定期校正。除此以外,我公司還用于對新模具進行終檢質量驗收,向模具制造車間和模具設計者反饋傾向和規律性數據用于改善相關工序。