拜耳法生產中經常用到苛性比、硅量指數、循環效率、晶種系數等概念。拜耳法就是用堿溶出鋁土礦中的氧化鋁。工業上把溶液中以NaAlO2和NaOH形式存在的Na2O叫做苛性堿(記作Na2Ok),以Na2CO3形式存在的Na2O叫做碳酸堿(記作Na2Oc),以Na2CO4形式存在的Na2O叫做硫酸堿(記作Na2O),所有形態的堿的總和稱做全堿(記作Na2Ot)。
苛性比就是鋁酸鈉溶液中的Na2Ok與Al2O3的摩爾比,記作αko。美國習慣用鋁酸鈉溶液中的Al2O3與Na2Ok的質量比表示,符號A/N。
硅量指數指鋁酸鈉溶液中的Al2O3與SiO2含量的比,符號A/S。
循環效率指鋁酸鈉溶液中的1t Na2O在一次拜耳法循環中產出的Al2O3的量(t),用E表示。它表明堿的利用率的高低。
晶種系數(種子比)指添加晶種氫氧化鋁中的Al2O3數量與分解原液中的Al2O3數量之比。
η=(1-αa/αm)×100%
式中 αa,αm-分別表示分解精液和分解母液的苛性比值。
拜耳法生產包括四個過程:(1)用αk=3.4的分解母液溶出鋁土礦中的氧化鋁,使溶出液的αk=1.6~1.5;(2)稀釋溶出液,洗滌分離出精制鋁酸溶液(精液);(3)精液加晶種分解;(4)分解母液蒸發濃縮至苛性堿的濃度達到溶出要求(230~280g/L)。拜耳法生產氧化鋁的工藝流程如圖1所示。
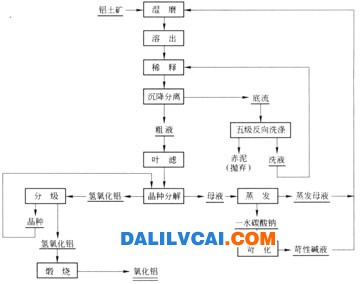
在這四個過程中,鋁土礦的溶出是拜耳法的關鍵工序。鋁土礦中的三水鋁石在140℃就很快地溶入苛性堿液,一水軟鋁石在180℃也就很快地溶入苛性堿液,而一水硬鋁石在240℃以上才較快地溶入苛性堿液,剛玉根本就不溶。為了使苛性堿溶液的溫度達到溶出所需溫度,就要用壓力釜給苛性堿液加熱。溶出氧化鋁的漿液的溫度和壓力都很高,需要取出其所含的能量,采用自蒸法產出二次蒸汽來預熱進入高壓釜前的漿液,同時降低了溶出液的溫度和壓力,流出高壓釜進入敞開容器洗滌、分離出鋁酸鈉精液。現代生產都是把一系列預熱器、高壓釜和自蒸發器串聯為溶出器組織進行連續作業。漿液靠高壓泵打入奪力釜,對于一水硬鋁石需達到3.33MPa/cm2以上的壓力。所以把高壓溶出車間比喻為氧化鋁生產過程的心臟。
拜耳法溶出時,為了減少結疤結瘤通常要進行脫硅,有在的原礦漿槽中于90℃以下的低溫脫硅和在150℃下進行的中溫脫硅,后者的脫硅效果較好,溶出液的硅量指數也較高。拜耳法溶液中Al2O3和SiO2濃度變化如圖2所示。
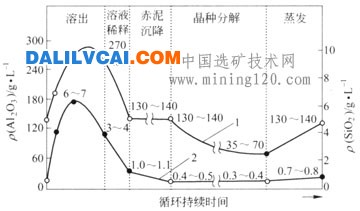
拜耳法要求鋁土礦中的Al2O3含量達55%以上,A/S越大越好。A/S從11降至7,生產成本將增加14.5%。我國的鋁土礦大多為A/S=5~7(占所有礦的59.3%),拜耳法不能經濟地處理。對這部分鋁土礦就要用堿石灰燒結法來處理。
由均化堆場送來的鋁土礦、石灰燒制工序送來的石灰,送入磨頭倉。鋁土礦、石灰和蒸發來的循環母液按一定配比進入由棒、球二段磨和水力旋流器組成的磨礦分級系統。水力旋流器溢流為合格原礦漿進入原礦漿槽。原礦漿經單套管預熱器送入預脫硅槽經8小時預脫硅后補入適當的循環堿液,達到正常堿配比由GEHO隔膜泵送入壓煮溶出多套管預熱系統。
礦漿經GEHO隔膜泵送入四套管預熱器,在壓煮器內加熱至250~260℃進行1小時溶出,溶出后礦漿經十一級自蒸發器閃蒸降溫,溶出礦漿用赤泥洗液稀釋。
稀釋礦漿在常壓脫硅槽進行4小時的常壓脫硅。脫硅后的稀釋礦漿在沉降槽內進行液固分離,底流進入洗滌沉降槽和深錐沉降槽組成的赤泥洗滌系統進行四次赤泥反向洗滌。制備好的絮凝劑經計量后分別加入分離和洗滌沉降槽,熱水加入末次洗滌槽。末次洗滌槽底流經泵送到赤泥堆場進行堆存,一次洗滌沉降槽溢流送至壓煮溶出稀釋槽。
分離沉降槽溢流經泵送粗液槽,再用粗液泵送往立式葉濾機喂料槽,在槽中加入定量的石灰乳作為助濾劑。含助濾劑的粗液用泵送到立式葉濾機進行控制過濾,濾餅送分離洗滌沉降槽,精液送板式熱交換器。
精液經三級板式熱交換器與分解母液和冷卻水進行熱交換冷卻到設定溫度。降溫后的精液與種子過濾濾餅(晶種)在晶種槽內混合,然后用晶種泵送至分解系列的首槽(1#或2#槽),經連續分解后從15#(或16#)槽頂用立式液下泵抽取分解漿液去進行旋流分級,分級前加入部分過濾母液稀釋,分級溢流進15#(或16#)分解槽,底流再用部分母液沖稀后自壓至產品過濾。分解末槽(14#或15#)的分解漿液從槽上部出料自流至立盤種子過濾機,濾餅用精液沖入晶種槽,濾液入錐形母液槽。
經分級底流的氫氧化鋁漿液經飼料泵送入平盤過濾機進行成品過濾并用蒸發送來的熱水進行洗滌。洗滌合格后的氫氧化鋁送焙燒爐進行焙燒,生產出合格氧化鋁。分離母液送種子過濾的錐形母液槽或分解槽末槽,氫氧化鋁洗液送赤泥沉降一次洗滌系統或分解錐形母液槽,溢流槽漿液經泵送到分解末槽。母液槽內的分解母液部分送氫氧化鋁分級用于稀釋水旋器進料和底流,其余經板式熱交換器與精液進行熱交換后送蒸發原液槽。
蒸發原液除少部分不經蒸發直接送母液調配槽外,其余絕大部分在蒸發器組內進行蒸發濃縮后送調配。蒸發原液首先經Ⅰ閃蒸后分別進入Ⅳ效和Ⅴ效,其中經Ⅳ效-Ⅲ效-Ⅱ效-Ⅰ效-Ⅱ閃-強制效的形式進行濃縮作業。鹽沉降槽溢流送到強堿槽(化清液),部分送各化學清洗用堿點和分解化學清洗槽,大部分返回與蒸發器Ⅴ效出料混合,通過出料泵送到母液槽;底流用過濾機進行過濾分離,濾液進鹽沉降槽溢流槽,然后進強堿液槽。
生產過程中消耗的堿,用液體燒堿或者片堿補充。卸下的液堿或者片堿,先送補堿槽,再到母液調配槽與蒸發母液、部分不經蒸發的原液及苛化稀液調配成符合濃度要求的循環母液

