摘要:簡單介紹了鋁型材擠壓成形的特點,對目前用于鋁型材擠壓仿真的
FEM 、FVM 技術進行了詳細地對比,對國內外鋁型材擠壓仿真技術的應用情況進
行了介紹和分析; 最后對專用鋁型材擠壓成形仿真軟件 HyperXtrude 的功能和應
用情況進行了介紹。
關鍵詞:鋁型材擠壓;仿真;HyperXtrude
1 引言
鋁型材產品由于具有重量輕、強度高、導電導熱性好、外形美觀、密封性好
等優點,被廣泛應用于建筑、車輛、船舶、飛機、通訊等各個領域,特別是建筑
門窗和幕墻,其發展速度遠遠高于其他金屬材料,在金屬產品中的消費量僅次于
鋼鐵[1]
。
擠壓成形是鋁型材生產的主導技術和核心環節, 擠壓模具是鋁型材擠壓成形
的關鍵裝備。在鋁型材擠壓過程中,模具結構不良容易導致型材扭擰、波浪、彎
曲以及裂紋等缺陷問題。 目前鋁型材擠壓模具的設計還停留在依靠工程類比和設
計經驗階段,所設計的模具必須經過反復的試模和修模來調整工藝參數,有的模
具試模次數達到 10 次以上,這嚴重影響了企業的模具開發周期和生產效率,影
響模具質量和模具壽命,增加了經濟成本和時間成本,因此改進傳統的模具設計
方法已經成為鋁型材及其模具廠家的當務之急。
大量的文獻資料顯示, 以有限元方法為代表的仿真技術正在成為優化鋁型材
模具的重要和必要的途徑。鋁型材擠壓過程是一個處在大變形、高溫、高壓、復
雜摩擦條件下的非線性成形過程, 采用物理實驗和現有的測量儀器與手段基本上
無法了解其中的成形機理和變形規律, 而運用仿真技術可以實時跟蹤鋁型材擠壓
金屬的流動行為,仿真成形過程,揭示金屬的真實流動規律和各種物理場量的分
布、變化情況,研究各種因素對金屬變形行為的作用和影響,預測實際擠壓過程
中可能出現的缺陷,及早優化模具結構設計、調整擠出工藝參數和有針對性的指
明技術解決方案,等等。因此,基于仿真技術的鋁型材擠壓成形及模具優化技術
得到越來越廣泛和深人的研究和應用。
本論文對鋁型材擠壓成形特點、擠壓成形仿真關鍵技術、國內外的研究應用
現狀等進行了詳細的論述,最后對專用鋁型材擠壓成形仿真軟件HyperXtrude 的
功能和應用情況進行了介紹。
2 鋁型材擠壓成形特點
鋁型材擠壓成形工藝過程可以看作是一種特殊的、復雜的流體運動過程,屬
于三維流動、非線性、大變形問題。在擠壓成形過程中,會不斷的產生新的自由
表面、產生新的熱量,發生溫度傳遞、大變形、復雜幾何形體變化等各種交叉藕
合現象;整個擠壓過程可以分為非穩態開始、穩態成形、非穩態結束三個階段,
在非穩態的擠壓變形階段,彈性變形由于遠遠小于金屬的塑性變形而可以被忽
略;但是在穩態變形階段,塑性變形不再劇烈的條件下,則必須考慮彈性變形的
影響,因此,其材料本構模型也非常復雜;同時,在高溫狀態下材料的粘度性能
不符合常粘度定律,材料的應變速率及溫度對變形的影響不可忽視。
模具是鋁型材擠壓成形的重要裝備,是決定鋁型材產品質量的先決條件之
一。鋁型材擠壓導流模的形狀和尺寸、分流腔的數量和分布、焊合室的形狀和深
度、定徑帶的長度、模具表面的光潔度等都會影響鋁合金在成形中的流動狀態,
進而影響型材擠出的質量。鋁型材制品尺寸越大、形狀越復雜,其變形的不均勻
性就越顯著,截面卜各部分的金屬在擠出??讜r的速度差異就越大,就越容易造
成型材的扭擰、波浪、彎曲及裂紋等缺陷[1]
。
3 鋁型材擠壓仿真技術
目前,鋁型材擠壓仿真所采用的技術主要有兩種,第一種是基于 Lagrange
格式的有限元方法(Finite Element Method , FEM ) ,第二種是基于 Euler
格式的有限體積法(Finite Volume Method , FVM )[2~3]
。
3.1 有限元方法(FEM)
FEM 的基本思想是將材料的整個求解域離散為一系列相互連接的單元體(如
三角形、四邊形或六面體等單元),通過求解各單元和節點在每一加載步上的物
理場量,來描述材料在成形過程中的變形情況。有限元方法必須滿足的基本方程
包括平衡方程、幾何方程、本構方程、屈服準則、體積不可壓縮條件、力和速度
邊界條件。
用有限元方法進行鋁型材擠壓成形仿真的優點是, 在計算過程中節點的位置
隨著成形的進行而不斷發生變化,單元的形狀也隨之發生變形,因而,節點與單
元瞬態的物理場量可以很好地描述成形體的變形情況。 這種方法不僅能很好處理
復雜邊界問題,而且能跟蹤材料變形節點,記憶材料變形的歷史,非常適合分析
瞬態成形問題。
用有限元方法方法進行鋁型材擠壓成形仿真的缺點是, 計算過程中網格會經
常發生畸變,導致體積損失過大,甚至出現網格無法生成的情況,必須對畸變后
的網格進行重新劃分,而這種方式既浪費計算時間,又降低了計算的精度,變形
程度大時甚至無法進行下去。
因此,有限元方法主要用于一些形狀相對簡單的鋁型材擠壓成形仿真,對于
復雜的鋁型材,特別是具有薄壁、空心、復雜斷面、高精度等特征的幕墻、門窗、
散熱器、壁板等復雜鋁型材,基本上沒有辦法進行仿真。
3.2 有限體積方法(FVM )
FVM 數值模擬的基本思想是將材料流動所要經歷的空間用 Euler 網格 (如六
面體網格)進行離散,Euler 網格的單元和中心格點在空間固定不動,材料只是
從一個單元流到另一個單元,并且材料的質量、動量和能量也隨之從一個單元流
到另一個單元,材料的變形行為則通過均布在材料中的大量質點來表述。使用
FVM 方法必須滿足質量守恒、動量守恒、能量守恒、本構關系、狀態方程和熱平
衡方程等控制方程。
用有限體積法進行鋁型材擠壓成形仿真的優點是, Euler 網格不隨材料一起
運動,因此網格在成形過程中不會發生畸變,求解過程中不需要進行網格重劃;
且采用直接積分和顯式求解方法,不需要迭代求解平衡方程,因此能處理各種復
雜程度的大變形問題,且計算時間相對較短。
用有限體積法進行鋁型材擠壓成形仿真的缺點是,在劃分網格單元時,劃分
范圍必須包括材料所有可能流過的區域,而且網格需要劃分得很細,因此采用有
限體積方法需要占用大量計算機內存,特別是對于具有薄壁、空心、復雜斷面等
特征的鋁型材需要占用更多的內存,因此這種方法對計算機硬件系統的要求極
高。而且,在有限元體積方法中,由于有限體積網格和中心格點在成形過程中固
定在空間不動,因此,它不能反映金屬成形過程中材料的整個流動情況,它只適
合分析邊界條件不變化的穩態問題, 不適合分析具有自由表面問題和依賴變形歷
史等特征的瞬態成形問題。
3.3 兩種方法的比較與應用
目前,兩種有限元方法在鋁型材擠壓成形仿真中都得到了應用,其中,基于
Lagrange 格式的有限元方法主要用于仿真坯料從擠壓開始時刻到擠出模具時刻
的非穩態階段,獲得擠壓型材頭部的變形情況以及擠壓缺陷等情況;Euler 格式
主要應用于穩態分析,即假設型材已經擠出模具,分析擠出型材的速度場、溫度
場以及應力應變等。
4 國內外鋁型材擠壓成形仿真技術應用現狀
國內外科研工作者在鋁型材擠壓仿真技術的研究和應用方面開展了很多工
作。
T.Chanda 等[4~7]
基于剛粘塑性成形理論,使用基于 FEM 的 DEFORM 系統研究
了簡單實心鋁合金模具擠壓過程中擠壓比和擠壓速度對坯料溫度變化的影響、 擠
壓載荷的變化情況、以及擠壓速度和型材溫度的關系等;Zhi Peng 等[8~9]
使用基
于 FEM 的 FORGE3 系統研究了多孔實心棒材擠壓時模孔對材料出口流動速度、溫度差異、變形力等的影響,分析了模具設計、擠壓工藝參數對產品質量(型材形
狀、表面質量和微觀組織)等的影響;
J.Lof
[10~11]
分別針對簡單薄壁空心筒形件和異形件,使用基于 ALE 描述
DiekA 代碼研究了模具工作帶內的材料行為、摩擦系數、工作帶長度情況,研究
了模具工作帶內的彈性變形的影響。
Chris Harris等[12~13]
使用DEFORM 系統研究了簡單形狀的鋁型材件擠壓成形
中的新舊棒材交接處的瞬態焊合現象進行了模擬, 導流模尺寸參數對金屬流動的
影響規律;
在國內,周飛等[14~16]
人對有限體積方法進行了深人研究,提出了將有限元方
法和有限體積方法相結合的復合方法,以及有限體積分步求解方法,并用于簡單
薄壁門窗型材模具的擠壓成形仿真;
吳向紅等人[17~19]
采用基于FVM 的Superforge系統對大口徑鋁管的平面分流
模擠壓過程進行了數值模擬,分析了擠壓過程中各個階段的應力、應變的分布情
況以及金屬的流動規律, 為大型鋁型材擠壓模具結構的設計和工藝參數的優化提
供了依據;對長方形空心鋁型材管擠壓過程進行了數值模擬和模具結構優化;研
究了擠壓速度和摩擦狀態對鋁型材擠壓過程中的模具受力、 擠壓件分度分布變化
以及材料流動速度的影響情況和影響規律。
于滬平等[20]
采用 DEFORM 系統對平面分流模的擠壓變形過程進行了二維模
擬, 得出了擠壓過程中鋁合金的應力、 應變、 溫度以及流動速度等的分布和變化;
陳澤中等人[21~23]
應用 Superforge 系統研究了復雜鋁型材擠壓成形過程,將
有限體積技術應用于寬展擠壓模具的設計中, 獲得了與實際金屬流出速度相符的
模擬結果;建立了基于正交試驗、人工神經網絡、遺傳算法的優化模型,對大型
實心鋁型材擠壓過程進行了模擬和優化, 獲得了最優的鋁型材擠壓工藝和模具參
數(模具工作帶長度、導流模的寬度和深度、模具預熱溫度、坯料預熱溫度、擠
壓速度)。
總結國內外的研究現狀發現, 目前的鋁型材模具擠壓仿真技術的發展和應用
情況具有以下特點:
1)目前國內用于鋁型材擠壓成形仿真的有限元系統主要有 DEFORM , MARC ,
ANSYS ,這些系統都是基于 Lagrange 格式的,DEFORM 是專業針對鍛造成形開發
的,ANSYS 和 MARC 是通用的綜合性分析軟件;基于 FEM 的鋁型材模具擠壓成形
主要是針對簡單、小型的鋁型材件,由于受到網格畸變和有限元程序網格重劃功
能的限制,對大型、復雜、薄壁的鋁型材模具的擠壓成形仿真結果不理想,甚至
無法實現;
2)于 FVM 的鋁型材模具擠壓成形仿真可以模擬一些復雜、大型、薄壁的鋁
型材的擠壓成形過程,但目前所用的有限體積仿真系統主要是 Superforge,該
系統基于 Euler 述,只能對瞬態成形階段進行模擬,得不到填充、焊合等非瞬態階段的變形和變形情況;且該軟件是專業針對鍛造成形開發的,無法正確描述鋁
型材成形過程中的分流、焊合等流體問題。雖然周飛等人將其他有限元分析系統
與 SuperForge 相結合,先用有限元仿真系統分析瞬態過程以后,再利用
Superforge 分析穩態過程,獲得了一些理想結果,但是有限元分析結束以后必
須進行三角形網格分解,同時將各物理場量傳遞到 FVM 仿真系統,這種不同仿
真系統之間的數據傳遞算法和精度仍然是值得探究的問題。
5 HyperXtrude 軟件介紹
如上所述,基于 Lagrange 格式和基于 Euler 格式的軟件系統各有利弊,且
利弊互補。為了發揮這兩種方法各自的優勢,出現了一種集成系統,也稱
Arbitrary Lagrange - Euler ( ALE )方法,這種系統將材料速度和網格速度
分開定義,空間網格可以設置成運動的,也可以設置成固定的,通過選擇網格的
運動形式就可以任意(arbitrary)指定是使用腸瞥朋羅描述還是 Euler,描述
來求解擠壓成形問題。
HyperXtrude 系統就是基于 ALE 描述的一款商用軟件系統。它是
HyperWorks 產品家族中的一員,也是由美國 Altair 公司開發的一個專用的鋁型
材模具擠壓仿真求解器。該軟件通過與前處理模塊 HyperMesh 和后處理模塊
Hyperview 結合,能夠實現對各種復雜程度的實心模和空心模的擠壓成形仿真,
求解擠壓過程中材料流動和熱傳遞的規律;能與優化模塊 HyperStudy 結合,實
現模具工作帶長度優化;該軟件針對鋁型材模具擠壓成形的特點,提供了很多智
能化的操作處理方式,比如廣泛的數據接口,擠壓筒、工件和模具的自動定義,
支持常見的擠壓型材材料本構關系,方便的邊界條件設置,數據結果的多種顯示
形式等等。
HyperXtrude 系統所具有的功能包括:
l )鋁型材擠壓變形仿真:可以仿真各種實心模和空心模的型材擠壓變形過
程,獲得擠壓過程中金屬應力、應變、溫度、流體速度等物理量的分布和變化情
況;
2 )鋁型材擠出的變形分析:能獲得擠出型材的變形情況;
3 )模具變形分析:分析計算模具的變形和模具內的應力分布情況;
4 )溫度場仿真分析:能夠定義坯料、模具和周圍環境之間的熱交換,計算
得到坯料內的熱傳導、擠壓筒和模具周圍熱傳遞、擠壓溫升和擠壓速度的關系。
5 )摩擦仿真:支持定義工件和模具之間、坯料和模腔之間的庫侖摩擦模型
或塑性剪切摩擦模型。
6 )棒料接口跟蹤分析,可以預測料尾長度;能夠跟蹤擠壓過程中坯料表面
并預測表皮雜質進人擠壓型材的時間。 7 )工作帶長度優化模塊,能以獲得均勻的工作帶型材流出速度為目標,優
化工作帶長度。
該軟件基于 ALE 描述,用戶可以根據需要選擇是對穩態階段還是非穩態階
段進行分析。
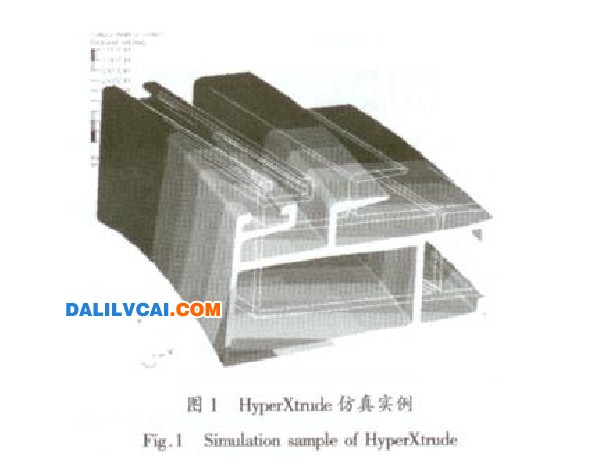
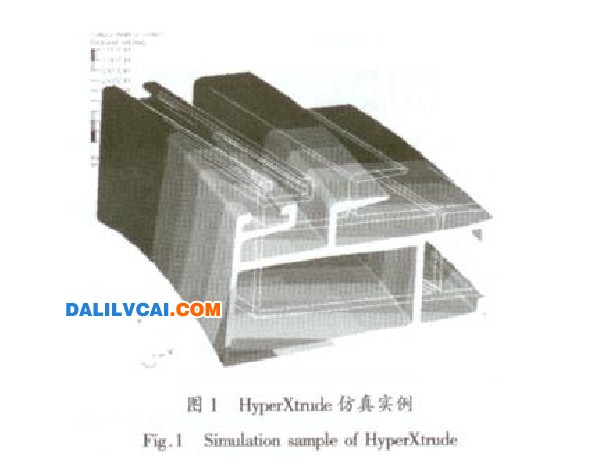
以下是運用 HyperXtrude 系統仿真分析得到的某空心鋁型材的型材變形趨
勢和程度,仿真結果顯示,型材變形很厲害。
6 結論
鋁型材產品不斷向著復雜、大型、高精、高強度等方向發展,模具設計的難
度越來越大, 利用仿真技術取代傳統的經驗開模和反復試模是未來鋁型材生產的
必要趨勢。 加快鋁型材擠壓仿真應用研究及其關鍵技術的深人研究是目前鋁型材
擠壓及其模具企業急需突破的核心技術,有待科研工作者結合實際,開展更廣泛
和更深入的調查研究。
利用仿真軟件實現鋁型材擠壓成形仿真技術的研究PDF高清版下載:
http://bbs.dalilvcai.com/Aluminum%20extrusion/thread-3316-1-1.html
利用仿真軟件實現鋁型材擠壓成形仿真技術的研究PDF高清版下載:
http://bbs.dalilvcai.com/Aluminum%20extrusion/thread-3316-1-1.html