摘要:對罐體拉伸工序、變薄拉伸工序和底部成形工序進行了分析,并對與這些工序相關的模具在設計和制造中存在的若干關鍵性技術進行了研究。
關鍵詞:易拉罐;成形工藝;模具;變薄拉伸
1 引 言
鋁質易拉罐在飲料包裝容器中占有相當大的比重。易拉罐的制造融合了冶金、化工、機械、電子、食品等諸多行業的先進技術,成為鋁深加工的一個縮影。隨著飲料包裝市場競爭的不斷加劇,對眾多制罐企業而言,如何在易拉罐生產中最大限度地減少板料厚度,減輕單罐質量,提高材料利用率,降低生產成本,是企業追求的重要目標。為此,以輕量化(light-weighting)為特征的技術改造和技術創新正在悄然興起。易拉罐輕量化涉及到許多關鍵性技術,其中罐體成形工藝和模具技術是十分重要的方面。
2 罐體制造工藝和技術
2.1罐體制造工藝流程
CCB-1A型罐罐體的主要制造工藝流程如下:卷料輸送→卷料潤滑→落料、拉伸→罐體成形→修邊→清洗/烘干→堆垛/卸→涂底色→烘干→彩印→底涂→烘干→內噴涂→內烘干→罐口潤滑→縮頸→旋壓縮頸。
在工藝流程中,落料、拉伸、罐體成形、修邊、縮徑、旋壓縮徑/翻邊工序需要模具加工,其中以落料、拉伸和罐體成形工序與模具最為關鍵,其工藝水平及模具設計制造水平的高低,直接影響易拉罐的質量和生產成本。
2.2罐體制造工藝分析
(1)落料一拉伸復合工序。拉伸時,坯料邊緣的材料沿著徑向形成杯,因此在塑性流動區域的單元體為雙向受壓,單向受拉的三向應力狀態,如圖1所示。由于受凸模圓弧和拉伸凹模圓弧的作用,杯下部壁厚約減薄10%,而杯口增厚約25%。杯轉角處的圓弧大小對后續工序(罐體成形)有較大的影響,若控制不好,易產生斷罐。因此落料拉伸工序必須考慮以下因素:杯的直徑和拉伸比、凸模圓弧、拉伸凹模圓弧、凸、凹模間隙、鋁材的機械性能、模具表面的摩擦性能、材料表面的潤滑、拉伸速度、突耳率等。突耳的產生主要由2個因素確定:一是金屬材料的性能,二是拉伸模具的設計。突耳出現在杯的最高點同時也是最薄點,將會對罐體成形帶來影響,造成修邊不全,廢品率增高。
基于以上分析,確定拉伸工序選擇的拉伸比m=36.55%,坯料直徑Dp=140.20±0.0lmm,杯直徑Dc=88.95mm。
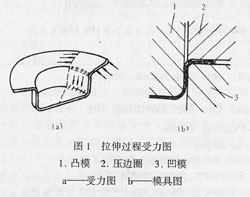
(2)罐體成形工序。
變薄拉伸工藝分析。典型的鋁罐拉伸、變薄拉伸過程如圖2所示,變薄拉伸過程中受力狀況如圖3所示。在拉伸過程中,集中在凹模口內錐形部分的金屬是變形區,而傳力區則為通過凹模后的筒壁及殼體底部。在變形區,材料處于軸向受拉、切向受壓、徑向受壓的三向應力狀態,金屬在三向應力的作用下,晶粒細化,強度增加,伴有加工硬化的產生。在傳力區,各部分材料受力狀況是不相同的,其中位于凸模圓角區域的金屬受力情況最為惡劣,其在軸向、切向兩向受拉,徑向受壓,因而材料的減薄趨勢嚴重,金屬易從此處發生斷裂,從而導致拉伸失敗。比較變形區和傳力區金屬的應力狀態可知:變薄拉伸工藝能否順利進行主要取決于拉伸凸模圓角部位的金屬所受拉應力的大小,當拉應力超過材料強度極限時就會引起斷裂,否則拉伸工藝可以順利進行。因此,減小拉伸過程中的拉應力成為保證拉伸順利進行的關鍵。
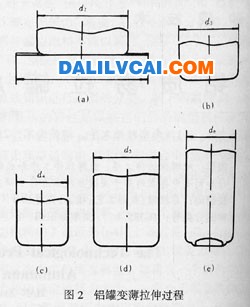
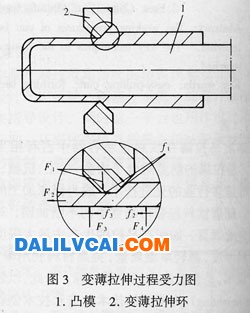
變薄拉伸拉伸比的選擇為:再拉伸:25.7%,第1次變薄拉伸:20%~25%,第2次變薄拉伸:23%~28%,第3次變薄拉伸:35%~40%。
在成形過程中,影響金屬內部所受拉應力大小的因素很多,其中凹模錐角。的取值直接關系到變形區金屬的流動特性,進而影響拉伸所需成形力的大小,所以,其數值合理與否對工藝的實施有著重要影響。當α較小時,變形區的范圍比較大,金屬易于流動,網格的畸變小。隨著α的增大,變形區的范圍減小,金屬的變形集中,流動阻力增大,網格歧變嚴重。而且,隨著凹模錐角的增大,變形區材料的應變相應增加,這說明凹模錐角較大時,不僅金屬的變形范圍集中,而且變形量迅速上升,因而使得變形區金屬的加工硬化現象加劇,導致金屬內部的應力上升,從而對拉伸產生不利影響。另一方面,在α過于大或過小時都會引起拉伸力的增加,其原因在于:當α過大時,金屬流動急劇,材料的加工硬化效應顯著,并且隨著錐角的增大,凹模錐面部分產生的阻礙金屬流動的分力加大,因而所需拉伸力增加;當。過小時,雖然金屬流動的轉折小,但由于變形區金屬與凹面的接觸錐面長,錐面上總摩擦阻力大,因此網格畸變雖小,總拉伸力卻增大。
由此可見,凹模錐角的合理確定應同時考慮變形區材料的變形特點以及模具與工件間的摩擦狀況,凹模錐角合理范圍的確定對拉伸工藝有著直接的影響。工藝試驗表明,對于CCB-1A型罐用鋁材3104H19,其凹模錐角合理取值在α=5°~8°為宜。
底部成形工藝分析。罐底部成形發生在凸模行程的終點,采用的是反向再拉伸工藝。圖4為罐底成形受力狀況示意圖,底部成形力主要取決于摩擦力的性質以及壓邊力的大小。通常,材料的厚度和強度是一對矛盾,材料愈薄,強度愈低,因此輕量化技術要求減少罐底直徑及設計特殊的罐底形狀。工藝試驗表明,罐底溝外壁夾角若α1大于40°,將大大減小罐底耐壓。考慮到金屬的成形性,凸模圓弧R不能小于3倍的料厚。但R太大,將會減小強度。球面和罐底溝內壁圓弧R1,至少為3倍料厚,通常R1取4~5倍料厚。減小罐底溝內壁夾角α2,將增加強度,生產中大多數采用10°以下。
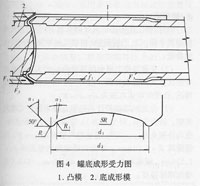
罐底部有兩處失效點:一為底部球面;二為連接球面和側壁的罐底部圓弧R。罐底球面的強度取決于以下幾個因素:材料的彈性模量、底部直徑、材料的強度、球面半徑以及在底部成形時金屬的變薄程度。罐底球面半徑常用公式R球=d1/0.77確定,實際取R球=45.72mm
3模具設計與制造
3.1罐體拉伸模
罐體拉伸過程實際上是筒形件的拉伸過程,拉伸過程中,其材料的凸緣部分在壓應力作用下易失穩,導致起皺,因此必須考慮設置防止起皺的壓邊裝置。當材料通過凹模時,凹模圓角部分是一個過渡區,其變形較復雜,除了徑向拉伸與切向壓縮外,還受彎曲作用,因此凹模圓角選擇尤為重要。材料通過凹模圓角后,處于拉伸狀態,由于拉伸力來自凸模壓力,是經過凸模圓角處傳遞的,凸模圓角處的材料變薄最嚴重,此處成為最易破裂的危險斷面。
落料一拉伸組合模結構如圖5所示。
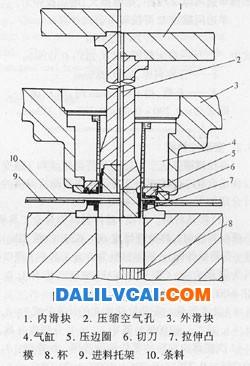
(1)模具材料:凸、凹模均選擇鑲硬質合金的材料。
(2)變形量:在易拉罐行業內,一般采用拉伸比δ表示變形量,δn=(dn-1—dn)/dn-1×100%,按此公式,計算如下:
首次拉伸取δ1=(d0—d1)/d0×100%=(140.2001—88.951)/140.2004×100%=36.6%。
再拉伸取δ2=(d1—d2)/d1×100%=(88.951—66.015)/88.951×100%=25.8%。
一般要求2次總拉伸比δ≤64%,δ1≥δ2≥……≥δn,δ1≤40%。
(3)壓邊裝置:采用波形壓邊圈,0.2—0.3MPa壓縮空氣作為動力源。
(4)拉伸模工作部參數:
圓角半徑:
拉伸凹模圓角半徑rA取3.556mm,再拉伸凹模圓角半徑rA取1.78mm。
拉伸凸模圓角半徑rB取2.921mm,再拉伸凸模圓角半徑取rB2.286mm。
間隙:
拉伸模凸、凹模單邊間隙Z/2大,則摩擦小,能減少拉伸力,但間隙大,精度不易控制;拉伸模凸、凹模單邊間隙Z/2小,則摩擦大,增加拉伸力。
單邊間隙Z/2可按以下公式計算:
Z/2=tmax+Kt
式中 tmax——最大料厚,取0.285+0.005mm
t——公稱料厚,取0.285mm
K——系數,當t<0.4mm時,取0.08
則Z/2=0.290+0.08×0.285=0.313mm。
3.2變薄拉伸模
易拉罐罐體成形實際上是將再拉伸和3道變薄拉伸組合在一起的組合工序。現將變薄拉伸模的設計介紹如下:
(1)模具材料。凸模:基體材料為合金工具鋼,凸模材料為M2,熱處理硬度60~62HRC,鍍TiN。凹模(變薄拉伸環):基體材料為合金工具鋼,模口材料為硬質合金(牌號為VALENITEVCID-H.L.D或KE-84KENNAMETAL)。
(2)變形量。變薄拉伸比方的計算公式為:δ=(tn-tn-1)/tn×100%,其中tn、tn-1分別為n次及n—1次變薄拉伸后的零件側面壁厚,計算得:δ1=(0.285—0.225)/0.285× 100%=21.05%;δ2=(0.225—0.170)/0.225×100%=24.44%;δ3=(0.170—0.106)/0.170×100%=37.65%。
制罐工廠常常根據給定的材料厚度、罐體厚、薄壁要求、拉伸環和凸模尺寸、拉伸機精度等條件,編制拉伸環和凸模的匹配表供技術人員、模具維修人員和操作人員選配凸模和拉環。
(3)模具的工作部分參數。凸模:凸模圓弧R1.016±0.025mm,再拉伸凸模圓弧R2.286mm,罐底溝外側壁圓弧R10.478±0.013mm。變薄拉伸環:凹模錐角α=5°,工作帶寬度h=0.38+0.25mm。
3.3罐底成形模
罐底成形模結構如圖6所示。
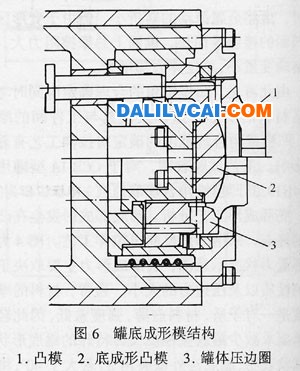
罐底凸模材料選用合金工具鋼Crl2MoV,熱處理硬度60~64HRC,其輪廓形狀應與罐型設計一致。底壓邊模材料選用合金工具鋼Cr5MoV,熱處理硬度58~60HRC,其輪廓形狀應與凸模相匹配。
4 結束語
(1)拉伸工序考慮的重要因素有:拉伸比、凸、凹模圓弧半徑、凸、凹模間隙、鋁材機械性能、潤滑、作業參數。
(2)變薄拉伸工序中凹模錐角。的大小關系到變形區金屬的流動性質、應力大小以及模具的受力情況,合理的取值范圍為α=5°—8°。
(3)合適的罐型設計是輕量化技術能否實施的關鍵。研究表明,對于CCB-1A型罐,設計參數選擇:底溝外壁夾角α1=32°,罐底溝內壁夾角α2=5°,凸模圓弧R=1.016mm,球面和罐底溝內壁圓弧R1=1.524mm,罐底球面半徑R球=45.72mm,可以大大增加罐體強度。
關鍵詞:易拉罐;成形工藝;模具;變薄拉伸
1 引 言
鋁質易拉罐在飲料包裝容器中占有相當大的比重。易拉罐的制造融合了冶金、化工、機械、電子、食品等諸多行業的先進技術,成為鋁深加工的一個縮影。隨著飲料包裝市場競爭的不斷加劇,對眾多制罐企業而言,如何在易拉罐生產中最大限度地減少板料厚度,減輕單罐質量,提高材料利用率,降低生產成本,是企業追求的重要目標。為此,以輕量化(light-weighting)為特征的技術改造和技術創新正在悄然興起。易拉罐輕量化涉及到許多關鍵性技術,其中罐體成形工藝和模具技術是十分重要的方面。
2 罐體制造工藝和技術
2.1罐體制造工藝流程
CCB-1A型罐罐體的主要制造工藝流程如下:卷料輸送→卷料潤滑→落料、拉伸→罐體成形→修邊→清洗/烘干→堆垛/卸→涂底色→烘干→彩印→底涂→烘干→內噴涂→內烘干→罐口潤滑→縮頸→旋壓縮頸。
在工藝流程中,落料、拉伸、罐體成形、修邊、縮徑、旋壓縮徑/翻邊工序需要模具加工,其中以落料、拉伸和罐體成形工序與模具最為關鍵,其工藝水平及模具設計制造水平的高低,直接影響易拉罐的質量和生產成本。
2.2罐體制造工藝分析
(1)落料一拉伸復合工序。拉伸時,坯料邊緣的材料沿著徑向形成杯,因此在塑性流動區域的單元體為雙向受壓,單向受拉的三向應力狀態,如圖1所示。由于受凸模圓弧和拉伸凹模圓弧的作用,杯下部壁厚約減薄10%,而杯口增厚約25%。杯轉角處的圓弧大小對后續工序(罐體成形)有較大的影響,若控制不好,易產生斷罐。因此落料拉伸工序必須考慮以下因素:杯的直徑和拉伸比、凸模圓弧、拉伸凹模圓弧、凸、凹模間隙、鋁材的機械性能、模具表面的摩擦性能、材料表面的潤滑、拉伸速度、突耳率等。突耳的產生主要由2個因素確定:一是金屬材料的性能,二是拉伸模具的設計。突耳出現在杯的最高點同時也是最薄點,將會對罐體成形帶來影響,造成修邊不全,廢品率增高。
基于以上分析,確定拉伸工序選擇的拉伸比m=36.55%,坯料直徑Dp=140.20±0.0lmm,杯直徑Dc=88.95mm。
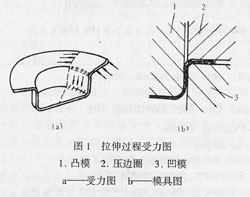
(2)罐體成形工序。
變薄拉伸工藝分析。典型的鋁罐拉伸、變薄拉伸過程如圖2所示,變薄拉伸過程中受力狀況如圖3所示。在拉伸過程中,集中在凹模口內錐形部分的金屬是變形區,而傳力區則為通過凹模后的筒壁及殼體底部。在變形區,材料處于軸向受拉、切向受壓、徑向受壓的三向應力狀態,金屬在三向應力的作用下,晶粒細化,強度增加,伴有加工硬化的產生。在傳力區,各部分材料受力狀況是不相同的,其中位于凸模圓角區域的金屬受力情況最為惡劣,其在軸向、切向兩向受拉,徑向受壓,因而材料的減薄趨勢嚴重,金屬易從此處發生斷裂,從而導致拉伸失敗。比較變形區和傳力區金屬的應力狀態可知:變薄拉伸工藝能否順利進行主要取決于拉伸凸模圓角部位的金屬所受拉應力的大小,當拉應力超過材料強度極限時就會引起斷裂,否則拉伸工藝可以順利進行。因此,減小拉伸過程中的拉應力成為保證拉伸順利進行的關鍵。
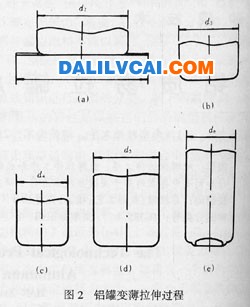
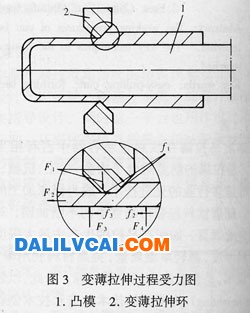
變薄拉伸拉伸比的選擇為:再拉伸:25.7%,第1次變薄拉伸:20%~25%,第2次變薄拉伸:23%~28%,第3次變薄拉伸:35%~40%。
在成形過程中,影響金屬內部所受拉應力大小的因素很多,其中凹模錐角。的取值直接關系到變形區金屬的流動特性,進而影響拉伸所需成形力的大小,所以,其數值合理與否對工藝的實施有著重要影響。當α較小時,變形區的范圍比較大,金屬易于流動,網格的畸變小。隨著α的增大,變形區的范圍減小,金屬的變形集中,流動阻力增大,網格歧變嚴重。而且,隨著凹模錐角的增大,變形區材料的應變相應增加,這說明凹模錐角較大時,不僅金屬的變形范圍集中,而且變形量迅速上升,因而使得變形區金屬的加工硬化現象加劇,導致金屬內部的應力上升,從而對拉伸產生不利影響。另一方面,在α過于大或過小時都會引起拉伸力的增加,其原因在于:當α過大時,金屬流動急劇,材料的加工硬化效應顯著,并且隨著錐角的增大,凹模錐面部分產生的阻礙金屬流動的分力加大,因而所需拉伸力增加;當。過小時,雖然金屬流動的轉折小,但由于變形區金屬與凹面的接觸錐面長,錐面上總摩擦阻力大,因此網格畸變雖小,總拉伸力卻增大。
由此可見,凹模錐角的合理確定應同時考慮變形區材料的變形特點以及模具與工件間的摩擦狀況,凹模錐角合理范圍的確定對拉伸工藝有著直接的影響。工藝試驗表明,對于CCB-1A型罐用鋁材3104H19,其凹模錐角合理取值在α=5°~8°為宜。
底部成形工藝分析。罐底部成形發生在凸模行程的終點,采用的是反向再拉伸工藝。圖4為罐底成形受力狀況示意圖,底部成形力主要取決于摩擦力的性質以及壓邊力的大小。通常,材料的厚度和強度是一對矛盾,材料愈薄,強度愈低,因此輕量化技術要求減少罐底直徑及設計特殊的罐底形狀。工藝試驗表明,罐底溝外壁夾角若α1大于40°,將大大減小罐底耐壓。考慮到金屬的成形性,凸模圓弧R不能小于3倍的料厚。但R太大,將會減小強度。球面和罐底溝內壁圓弧R1,至少為3倍料厚,通常R1取4~5倍料厚。減小罐底溝內壁夾角α2,將增加強度,生產中大多數采用10°以下。
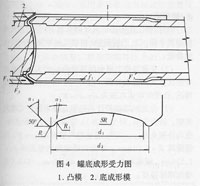
罐底部有兩處失效點:一為底部球面;二為連接球面和側壁的罐底部圓弧R。罐底球面的強度取決于以下幾個因素:材料的彈性模量、底部直徑、材料的強度、球面半徑以及在底部成形時金屬的變薄程度。罐底球面半徑常用公式R球=d1/0.77確定,實際取R球=45.72mm
3模具設計與制造
3.1罐體拉伸模
罐體拉伸過程實際上是筒形件的拉伸過程,拉伸過程中,其材料的凸緣部分在壓應力作用下易失穩,導致起皺,因此必須考慮設置防止起皺的壓邊裝置。當材料通過凹模時,凹模圓角部分是一個過渡區,其變形較復雜,除了徑向拉伸與切向壓縮外,還受彎曲作用,因此凹模圓角選擇尤為重要。材料通過凹模圓角后,處于拉伸狀態,由于拉伸力來自凸模壓力,是經過凸模圓角處傳遞的,凸模圓角處的材料變薄最嚴重,此處成為最易破裂的危險斷面。
落料一拉伸組合模結構如圖5所示。
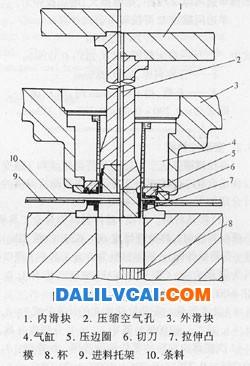
(1)模具材料:凸、凹模均選擇鑲硬質合金的材料。
(2)變形量:在易拉罐行業內,一般采用拉伸比δ表示變形量,δn=(dn-1—dn)/dn-1×100%,按此公式,計算如下:
首次拉伸取δ1=(d0—d1)/d0×100%=(140.2001—88.951)/140.2004×100%=36.6%。
再拉伸取δ2=(d1—d2)/d1×100%=(88.951—66.015)/88.951×100%=25.8%。
一般要求2次總拉伸比δ≤64%,δ1≥δ2≥……≥δn,δ1≤40%。
(3)壓邊裝置:采用波形壓邊圈,0.2—0.3MPa壓縮空氣作為動力源。
(4)拉伸模工作部參數:
圓角半徑:
拉伸凹模圓角半徑rA取3.556mm,再拉伸凹模圓角半徑rA取1.78mm。
拉伸凸模圓角半徑rB取2.921mm,再拉伸凸模圓角半徑取rB2.286mm。
間隙:
拉伸模凸、凹模單邊間隙Z/2大,則摩擦小,能減少拉伸力,但間隙大,精度不易控制;拉伸模凸、凹模單邊間隙Z/2小,則摩擦大,增加拉伸力。
單邊間隙Z/2可按以下公式計算:
Z/2=tmax+Kt
式中 tmax——最大料厚,取0.285+0.005mm
t——公稱料厚,取0.285mm
K——系數,當t<0.4mm時,取0.08
則Z/2=0.290+0.08×0.285=0.313mm。
3.2變薄拉伸模
易拉罐罐體成形實際上是將再拉伸和3道變薄拉伸組合在一起的組合工序。現將變薄拉伸模的設計介紹如下:
(1)模具材料。凸模:基體材料為合金工具鋼,凸模材料為M2,熱處理硬度60~62HRC,鍍TiN。凹模(變薄拉伸環):基體材料為合金工具鋼,模口材料為硬質合金(牌號為VALENITEVCID-H.L.D或KE-84KENNAMETAL)。
(2)變形量。變薄拉伸比方的計算公式為:δ=(tn-tn-1)/tn×100%,其中tn、tn-1分別為n次及n—1次變薄拉伸后的零件側面壁厚,計算得:δ1=(0.285—0.225)/0.285× 100%=21.05%;δ2=(0.225—0.170)/0.225×100%=24.44%;δ3=(0.170—0.106)/0.170×100%=37.65%。
制罐工廠常常根據給定的材料厚度、罐體厚、薄壁要求、拉伸環和凸模尺寸、拉伸機精度等條件,編制拉伸環和凸模的匹配表供技術人員、模具維修人員和操作人員選配凸模和拉環。
(3)模具的工作部分參數。凸模:凸模圓弧R1.016±0.025mm,再拉伸凸模圓弧R2.286mm,罐底溝外側壁圓弧R10.478±0.013mm。變薄拉伸環:凹模錐角α=5°,工作帶寬度h=0.38+0.25mm。
3.3罐底成形模
罐底成形模結構如圖6所示。
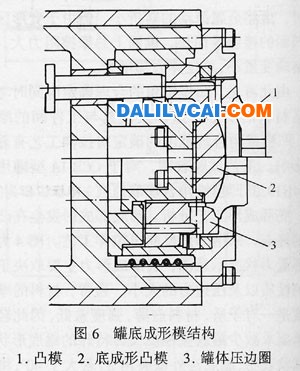
罐底凸模材料選用合金工具鋼Crl2MoV,熱處理硬度60~64HRC,其輪廓形狀應與罐型設計一致。底壓邊模材料選用合金工具鋼Cr5MoV,熱處理硬度58~60HRC,其輪廓形狀應與凸模相匹配。
4 結束語
(1)拉伸工序考慮的重要因素有:拉伸比、凸、凹模圓弧半徑、凸、凹模間隙、鋁材機械性能、潤滑、作業參數。
(2)變薄拉伸工序中凹模錐角。的大小關系到變形區金屬的流動性質、應力大小以及模具的受力情況,合理的取值范圍為α=5°—8°。
(3)合適的罐型設計是輕量化技術能否實施的關鍵。研究表明,對于CCB-1A型罐,設計參數選擇:底溝外壁夾角α1=32°,罐底溝內壁夾角α2=5°,凸模圓弧R=1.016mm,球面和罐底溝內壁圓弧R1=1.524mm,罐底球面半徑R球=45.72mm,可以大大增加罐體強度。
(1)拉伸工序考慮的重要因素有:拉伸比、凸、凹模圓弧半徑、凸、凹模間隙、鋁材機械性能、潤滑、作業參數。 答案補充
2)變薄拉伸工序中凹模錐角。的大小關系到變形區金屬的流動性質、應力大小以及模具的受力情況,合理的取值范圍為α=5°-8°。 (3)合適的罐型設計是輕量化技術能否實施的關鍵。研究表明,對于CCB-1A型罐,設計參數選擇:底溝外壁夾角α1=32°,罐底溝內壁夾角α2=5°,凸模圓弧R=1.016mm,球面和罐底溝內壁圓弧R1=1.524mm,罐底球面半徑R球=45.72mm,可以大大增加罐體強度。