1 概述
伴隨著全球金融危機的影響,石油資源給傳統汽車帶來越來越大的約束,為了擺脫這種窘境,許多國內外汽車廠商都宣布了進軍新能源汽車領域的計劃。國內外的汽車主機廠紛紛在混合動力、太陽能、電能等等新能源上研發新能源汽車。
在國內,比亞迪公司作為電能存放技術與汽車制造技術的領跑者,在新能源汽車方面一直保持著較快的發展勢頭。比亞迪E6電動車,是一款純電動四驅車型,動力與啟動電池均采用比亞迪自主生產的ET-POWER鐵電池,百公里加速時間在14秒以內,充電一次大致需要7個小時,續航能力超過300公里。
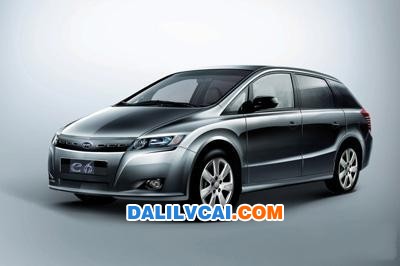
圖1 比亞迪E6電動車
現代汽車行業節能減排的呼聲越來越強烈,對汽車輕量化的要求也變得更加迫切。這里我們以汽車輪轂為例展開論述,鋁合金輪轂以其質量輕、強度高、可靠性可塑性強、價格適中、外觀時尚等特點已經成為汽車行業的首選。
據美國金屬市場統計,近10年來世界每輛汽車平均用鋁量增加了2倍,2001年世界每輛汽車平均用鋁量已達113.5kg,特別是北美汽車用鋁量增長最快,2002年北美生產的汽車平均每輛用鋁量達124kg左右。
預計2010年,汽車輪轂的鋁化率可達72%-78%,不過,低壓永久模鑄造的輪轂仍占主導,約占輪轂總量的75%左右。
據美國金屬市場統計,近10年來世界每輛汽車平均用鋁量增加了2倍,2001年世界每輛汽車平均用鋁量已達113.5kg,特別是北美汽車用鋁量增長最快,2002年北美生產的汽車平均每輛用鋁量達124kg左右。
預計2010年,汽車輪轂的鋁化率可達72%-78%,不過,低壓永久模鑄造的輪轂仍占主導,約占輪轂總量的75%左右。
2 國內鋁合金輪轂的生產現狀
經過幾十年的建設,我國汽車工業已初具規模,09年10月在長春一汽一輛金橙色解放J6的下線,是我國該年第1000萬輛汽車誕生,標志著我國成為繼美國、日本之后,第三個汽車年產銷量超過千萬的國家。
同時,鋁合金輪轂作為汽車輕量化產品,在我國已引起廣泛重視,國內鋁合金輪轂市場主要集中在南北大眾、廣本和幾個微型車廠、皮卡等主機廠,近幾年,國際市場對鋁合金輪轂的需求也一直看好,我國產品已高性價比出口美國、日本、韓國等地。中國有25家鑄造鋁合金輪轂廠,年生產能約2000萬件, 2002的的產量1400萬件,其中出口600萬件。
中國首條鍛造鋁合金輪轂生產線正在戴卡鋁輪轂有限公司建設,可于今年晚些時候投產,有2臺鍛壓機,年生產能力100萬件。戴卡公司是中國首家鋁輪轂企業,為中國汽車輪轂鋁化作出了重要貢獻。
同時,鋁合金輪轂作為汽車輕量化產品,在我國已引起廣泛重視,國內鋁合金輪轂市場主要集中在南北大眾、廣本和幾個微型車廠、皮卡等主機廠,近幾年,國際市場對鋁合金輪轂的需求也一直看好,我國產品已高性價比出口美國、日本、韓國等地。中國有25家鑄造鋁合金輪轂廠,年生產能約2000萬件, 2002的的產量1400萬件,其中出口600萬件。
中國首條鍛造鋁合金輪轂生產線正在戴卡鋁輪轂有限公司建設,可于今年晚些時候投產,有2臺鍛壓機,年生產能力100萬件。戴卡公司是中國首家鋁輪轂企業,為中國汽車輪轂鋁化作出了重要貢獻。
鋁合金輪轂是一種材料密集型、勞動力密集型的低附加值產品,由于鋁合金輪轂的高投入高產出的行業特點,許多企業因為缺乏關鍵技術,只重視設備的引進,造成了生產能力難以發揮,成品率低,產品缺乏競爭力,最終被市場淘汰。
3 國內鋁合金輪轂的工藝狀況
鋁合金輪轂的生產工藝主要有鍛造和鑄造兩種,鍛造工藝比鑄造工藝強度高18%以上,重量輕15%,但生產工藝和成本較高,目前鋁合金輪轂以鑄造為主,其中低壓鑄造工藝約占全部產量的80%以上,重力鑄造工藝約占20%,另外還有擠壓鑄造工藝等。
低壓鑄造工藝主要有以下優點:
1.液體金屬充型比較平穩;
2.鑄件成形性好,有利于形成輪廓清晰、表面光潔的鑄件,對于大型薄壁鑄件的成形更為有利;
3.鑄件組織致密,機械性能高;
4.提高了金屬液的工藝收得率,一般情況下不需要冒口,使金屬液的收得率大大提高,收得率一般可達90%。
此外,勞動條件好;設備簡單,易實現機械化和自動化,也是低壓鑄造的突出優點。
4 低壓鑄造軟件分析
低壓鑄造的工藝規范包括預壓、充型、增壓、飽壓、模具預熱溫度、澆注溫度,以及模具的涂料等。以AnyCasting為分析工具,通過對模具溫度、壓力規范和冷卻條件的模擬,預測和分析充型和凝固過程中的問題,實現鋁合金輪轂低壓鑄造工藝的優化。
將輪轂和模具等部件的三維模型(如圖2、3),輪轂外形尺寸為415mm×415mm×178mm,由part轉為STL文件導入分析工具后,設置各部件屬性(鑄件型腔、流道、渣包、模具、附件等等)。所選工藝參數:鋁液澆注溫度700±10℃,模具溫度480℃,界面換熱系數(gm/s3/K):鑄件/鑄型為3.0×105(有保溫涂料)。

圖2 輪轂三維造型
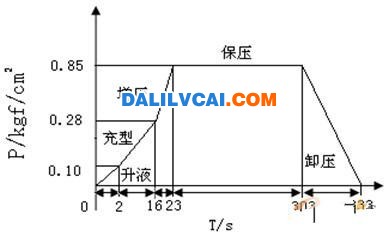
圖3 低壓鑄造壓力曲線
通過模擬發現充型過程中發生了噴濺現象,預測了充型壓力曲線存在的問題。
5 結論
隨著計算機性能和信息技術的不斷進步,制造業的數字化以及仿真模擬的技術也日趨完善。在鑄造過程仿真模擬行業中,出現了ProCAST、MAGMA、Flow-3D、dieCAS、AnyCasting、華鑄等等非常成熟的商業軟件。仿真軟件的發展,給傳統的制造行業注入了強勁的動力,同時也得到越來越多的企業的認可和應用。