1 引言
隨著科學技術的進步,對鑄件的內在質量和外觀質量都提出了更高的要求。汽車等行業對鑄件的要求向薄壁、形狀復雜、高強度、高質量的方向發展,使得鑄造鋁合金近年來發展迅速。鋁硅合金的枝晶不發達,結品溫度間隔是幾類鑄造鋁合金中最小的,在凝固過程開始后的一段時間內,合金液仍可流動,并且在固相線附近的溫度下有較高的強度,因而在鑄造鋁合金中其鑄造性能是最好的。但易產生集中縮孔,故必須設置較大冒口補縮;鋁合金中的一些元素化學性質都比較活潑,不僅在熔煉過程中易氧化,在澆注過程中,二次氧化的傾向也很大,極易形成氧化夾渣;此外鋁合金液有較強的吸氣傾向,很容易和水反應而出現鑄件的針孔現象。
針對杭州杭氧鑄造有限公司在采用重力澆注試制生產鋁硅合金箱休類鑄件中存在的氧化夾渣、氣孔、針孔、縮松等缺陷的情況,改用低壓鑄造工藝,獲得了良好的效果,實現了合格鑄件的批量生產。
鑄件簡介及質量要求
本箱體是某國內知名上市公司的工程車的重要零部件,該鑄件形狀較復雜、壁厚不均勻、結構緊奏,材質是ZL111,最大外形尺寸450mm×585mm×315 mm,最厚壁厚為60mm,基本壁厚為14mm,鑄件重約50kg。質量要求:鑄件不得有氣孔、夾渣、縮孔、裂紋、縮松等缺陷,水壓0.3MPa、試壓l5min,不得有泄漏現象。該鑄件在我公司試制生產前,由于鑄件質量得不到保證,以至從歐美進口。通過多次生產試驗,改變工藝技術方案,成功地解決了相關技術問題,使該鑄件成功實現了國產化,替代了進口產品,并成功返銷國外,創造了良好的經濟效益和社會效益。
2 箱體工藝方案的分析
2.1 重力澆注工藝的質t問題
該箱體鑄件是典型的殼體類鋁硅合金鑄件,結構較復雜,厚薄差異大,在采用重力澆注工藝的情況下盡管放了很多冷鐵、冒口和出氣,但廢品率仍然很高,經常在鑄件上出現氧化夾渣、氣孔、縮松等缺陷。
2.2 低壓鑄造工藝的擬定
針對重力澆注出現的質量問題,為了生產出合格的鑄件,經過詳細技術分析后,改用低壓鑄造工藝鑄造,采用樹脂砂兩箱造型和開放式澆注系統,工藝簡圖如圖1所示。在進行低壓鑄造工藝設計時,本鑄件采用了穩壓凝固工藝鑄造技術,其工藝特點是:升液速度緩慢,充型速度稍快,凝固壓力小,合金液充滿型后即保持在充型壓力下或稍高充型壓力下結晶凝固,直到鑄件完全凝固后放氣解壓。穩壓凝固工藝如圖2所示。
圖1 箱體鑄造工藝圖
圖2 箱體低壓穩壓工藝
澆注溫度的選定原則與一般澆注法相同,在保證成型的前提下,應該越低越好,本鑄件的澆注溫度取680℃-710℃。
2.2.2 充型壓力和充型速度
充型壓力和充型速度是低壓鑄造的主要工藝參數,直接影響鑄件質量。當充型速度太快時,型腔中氣體來不及排出,就會產生鑄件輪廓不清、氣孔或澆不到等缺陷;如果充型速度太慢,合金液溫度下降,粘度增大,充型能力降低,也會導致鑄件冷隔、澆不到等缺陷。根據巴斯葛原理P=μHρg,計算出充型壓力為0.12MPa-0.16MPa。充型時間為15s-30s。
2.2.3 增壓和增壓速度
鑄件的凝固壓力應該比充型壓力大,實踐表明,凝固壓力越大,補縮效果越好,獲得的鑄件組織越致密,但是,若采用過高的凝固壓力,不僅會影響鑄件的尺寸精度和表面粗糙度,甚至會造成鑄件粘砂和脹箱,由于本鑄件質量要求高,根據經驗取凝固壓力為0.l3MPa-0.16MPa,增壓速度為0.003MPa-0.006MPa/s。
2.2.4 保壓時間
保壓時間通常以鑄件內澆道處無縮孔或澆道殘留40mm左右所需的時間為宜。取本件的保壓時間為10min-15min。
2.2.5 鑄造模擬
利用華鑄CAE凝固模擬分析軟件驗證并完善工藝方案,模擬凝固過程的液相分布符合工藝要求,如圖3所示。
圖3 鑄件的三維凝固模型
此鑄件在鑄造過程中除了要按照以上方案實施外,還應達到以下要求:
(l)造型時上箱鑄型高點和出氣死角處均需放φ3mm的出氣。
(2)放置的冷鐵工作面必須清潔無污染。
(3)鑄型表面、坭芯、冷鐵涂刷涂料兩遍,刷涂料前鑄型需放置4h后進行,以利于砂型水分揮發。
(4)合箱前冷鐵表面需烘烤以去除水分,合箱后馬上澆注。
(5)嚴格控制熔煉操作工藝規程。
通過嚴格控制操作規程、完善工藝規范,使得本鑄件成功進人了穩定的批量生產,產品質量達到各項檢驗標準要求。
3 結束語
用低壓鑄造此類鋁硅殼體鑄件,合金液充型平穩,減少了合金液的飛濺、氧化夾渣、氣孔等缺陷。提高了鑄件的合格率。同時,一方面由于鑄件是在壓力作用下進行結晶凝固,大大地改進了補縮效果,獲得了組織致密的鑄件,這對于具有耐壓和防滲漏等工作要求的鑄件效果明顯。另一方面,由于低壓鑄造利用壓力充型和補縮,大大地簡化了澆冒口系統結構,提高了工藝出品率。
隨著科學技術的進步,對鑄件的內在質量和外觀質量都提出了更高的要求。汽車等行業對鑄件的要求向薄壁、形狀復雜、高強度、高質量的方向發展,使得鑄造鋁合金近年來發展迅速。鋁硅合金的枝晶不發達,結品溫度間隔是幾類鑄造鋁合金中最小的,在凝固過程開始后的一段時間內,合金液仍可流動,并且在固相線附近的溫度下有較高的強度,因而在鑄造鋁合金中其鑄造性能是最好的。但易產生集中縮孔,故必須設置較大冒口補縮;鋁合金中的一些元素化學性質都比較活潑,不僅在熔煉過程中易氧化,在澆注過程中,二次氧化的傾向也很大,極易形成氧化夾渣;此外鋁合金液有較強的吸氣傾向,很容易和水反應而出現鑄件的針孔現象。
針對杭州杭氧鑄造有限公司在采用重力澆注試制生產鋁硅合金箱休類鑄件中存在的氧化夾渣、氣孔、針孔、縮松等缺陷的情況,改用低壓鑄造工藝,獲得了良好的效果,實現了合格鑄件的批量生產。
鑄件簡介及質量要求
本箱體是某國內知名上市公司的工程車的重要零部件,該鑄件形狀較復雜、壁厚不均勻、結構緊奏,材質是ZL111,最大外形尺寸450mm×585mm×315 mm,最厚壁厚為60mm,基本壁厚為14mm,鑄件重約50kg。質量要求:鑄件不得有氣孔、夾渣、縮孔、裂紋、縮松等缺陷,水壓0.3MPa、試壓l5min,不得有泄漏現象。該鑄件在我公司試制生產前,由于鑄件質量得不到保證,以至從歐美進口。通過多次生產試驗,改變工藝技術方案,成功地解決了相關技術問題,使該鑄件成功實現了國產化,替代了進口產品,并成功返銷國外,創造了良好的經濟效益和社會效益。
2 箱體工藝方案的分析
2.1 重力澆注工藝的質t問題
該箱體鑄件是典型的殼體類鋁硅合金鑄件,結構較復雜,厚薄差異大,在采用重力澆注工藝的情況下盡管放了很多冷鐵、冒口和出氣,但廢品率仍然很高,經常在鑄件上出現氧化夾渣、氣孔、縮松等缺陷。
2.2 低壓鑄造工藝的擬定
針對重力澆注出現的質量問題,為了生產出合格的鑄件,經過詳細技術分析后,改用低壓鑄造工藝鑄造,采用樹脂砂兩箱造型和開放式澆注系統,工藝簡圖如圖1所示。在進行低壓鑄造工藝設計時,本鑄件采用了穩壓凝固工藝鑄造技術,其工藝特點是:升液速度緩慢,充型速度稍快,凝固壓力小,合金液充滿型后即保持在充型壓力下或稍高充型壓力下結晶凝固,直到鑄件完全凝固后放氣解壓。穩壓凝固工藝如圖2所示。
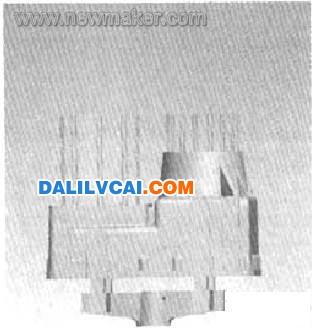
圖1 箱體鑄造工藝圖
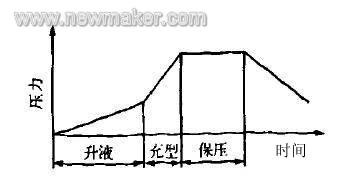
圖2 箱體低壓穩壓工藝
2.2.1 澆注溫度
澆注溫度的選定原則與一般澆注法相同,在保證成型的前提下,應該越低越好,本鑄件的澆注溫度取680℃-710℃。
2.2.2 充型壓力和充型速度
充型壓力和充型速度是低壓鑄造的主要工藝參數,直接影響鑄件質量。當充型速度太快時,型腔中氣體來不及排出,就會產生鑄件輪廓不清、氣孔或澆不到等缺陷;如果充型速度太慢,合金液溫度下降,粘度增大,充型能力降低,也會導致鑄件冷隔、澆不到等缺陷。根據巴斯葛原理P=μHρg,計算出充型壓力為0.12MPa-0.16MPa。充型時間為15s-30s。
2.2.3 增壓和增壓速度
鑄件的凝固壓力應該比充型壓力大,實踐表明,凝固壓力越大,補縮效果越好,獲得的鑄件組織越致密,但是,若采用過高的凝固壓力,不僅會影響鑄件的尺寸精度和表面粗糙度,甚至會造成鑄件粘砂和脹箱,由于本鑄件質量要求高,根據經驗取凝固壓力為0.l3MPa-0.16MPa,增壓速度為0.003MPa-0.006MPa/s。
2.2.4 保壓時間
保壓時間通常以鑄件內澆道處無縮孔或澆道殘留40mm左右所需的時間為宜。取本件的保壓時間為10min-15min。
2.2.5 鑄造模擬
利用華鑄CAE凝固模擬分析軟件驗證并完善工藝方案,模擬凝固過程的液相分布符合工藝要求,如圖3所示。
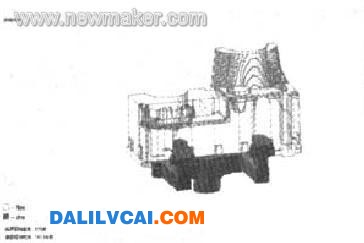
圖3 鑄件的三維凝固模型
2.2.6 操作要求
此鑄件在鑄造過程中除了要按照以上方案實施外,還應達到以下要求:
(l)造型時上箱鑄型高點和出氣死角處均需放φ3mm的出氣。
(2)放置的冷鐵工作面必須清潔無污染。
(3)鑄型表面、坭芯、冷鐵涂刷涂料兩遍,刷涂料前鑄型需放置4h后進行,以利于砂型水分揮發。
(4)合箱前冷鐵表面需烘烤以去除水分,合箱后馬上澆注。
(5)嚴格控制熔煉操作工藝規程。
通過嚴格控制操作規程、完善工藝規范,使得本鑄件成功進人了穩定的批量生產,產品質量達到各項檢驗標準要求。
3 結束語
用低壓鑄造此類鋁硅殼體鑄件,合金液充型平穩,減少了合金液的飛濺、氧化夾渣、氣孔等缺陷。提高了鑄件的合格率。同時,一方面由于鑄件是在壓力作用下進行結晶凝固,大大地改進了補縮效果,獲得了組織致密的鑄件,這對于具有耐壓和防滲漏等工作要求的鑄件效果明顯。另一方面,由于低壓鑄造利用壓力充型和補縮,大大地簡化了澆冒口系統結構,提高了工藝出品率。